Panizzolo Software:
For smart and easy management and monitoring of the treatment flow
The use of automated processes for in-line treatment of metal scrap is a known topic, though few companies take advantage of it. This is why Panizzolo Recycling integrates its software in its recycling plants so as to help you to exploit your metals fully.

The use of automated processes for in-line treatment of metal scrap is a known topic, though few companies take advantage of it. This is why Panizzolo Recycling integrates its software in its recycling plants so as to help you to exploit your metals fully. Thanks to our first-hand experience, we have analysed the parameters that directly affect the processing cycle and have programmed a software that helps customers meet their production goals. Panizzolo software gives you full control in monitoring absorptions, measurements, working pressures and all of those data that characterise normal operation of the plant. All on your own, either on the machine or remotely.
Operators shall simply and intuitively be able to start and stop machinery in full safety, adjust and save processing parameters, remember the periodic inspections and maintenance, anticipate faults, avoid overloads, make use of remote assistance and much more.
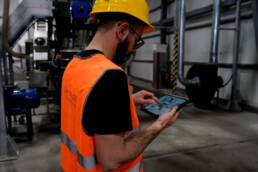
Tracking the production process, even remotely, allows you to immediately change the most important parameters of the treatment cycle.To do so, you may interact with the plant from the specific last generation touch screen panel or by tablet or smartphone.
Just one software for a real-time view
The functions that allow you to make the difference in daily management.
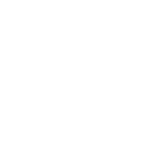
Monitoring
This section is the cornerstone for proper operation of the production cycle. It is possible to monitor data such as electric absorption, overall power, processing status, the activity of components, the performance of electric motors, automatic adjustment interventions and much more. The simple and intuitive layout of the information allows operators to control the entire production process, anticipating overloads or anomalous behaviour.
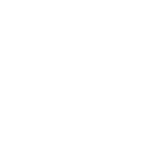
Safety and alarms
The safety system was designed according to the operating logic of the plant. The software dialogues with visual indicators and individual electronic and mechanical systems integrated in specific zones. The main objectives are the safety of the operators and a clear identification of the problem, so that you may have a complete diagnosis and know what to do to be able to restart as quickly as possible. Essential measures – such as line circuit breakers and watertight switchgear with air-to-air heat exchanger and holding of internal temperature – bring the essential components of Panizzolo plants to a higher safety level.
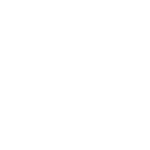
Energy Analyzer
Particularly attentive to the customer’s business, we are aware of the importance of having an overall view of the plant’s electricity consumption. Special analysers monitor the consumption and record voltage drops and overcurrents. This data is processed by Panizzolo’s Software in order to have a comprehensive analysis of the daily, periodic or actual consumption of a given process. This system is particularly useful for monitoring the voltage drops and the quality of the current input into the electric panel.
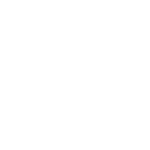
Processing settings
Panizzolo software has an advanced setting area, allowing to define specific parameters to optimise processing of infeed metal scrap. This is aimed at promoting constant production cycles, maximising production performance and keeping the items from overloading. Thanks to our first-hand experience, we can be at your side for the best setting of the production line, allowing you to find the right balance between infeed and outfeed quantity to the benefit of the quality of the final output and the long-term integrity of the components. The Panizzolo quality service includes the professional training of operators, for correct and efficient use of the recycling solution.
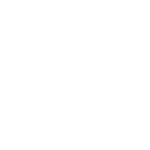
Maintenance
Thanks to the pre-adjusted setting and to specific visual notifications, you can schedule all routine inspection and maintenance operations in advance. At Panizzolo, we are convinced advocates of the concept of predictive maintenance since constant attention to the condition of the components really extends the lifetime of the machinery and its processing quality, tangibly saving time and money through the years. Our goal is to accompany you to the full knowledge of the maintenance activities to be carried out so that you can constantly keep your technological investment “healthy”.
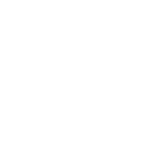
Troubleshooting
The treatment of metal scrap is, by its very nature, a type of processing which can subject the machinery to stress and wear on the long-term. This is why Panizzolo software includes a specific diagnostics area which, through digital and synoptic interactions of the plant, displays both technical information and anomalies. There is a dedicated section next to the real-time alarms that stores their history, that can be downloaded for more extensive analysis.
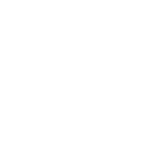
Remote assistance
The software can be connected to the Internet, by means of a network cable, for remote assistance.
Panizzolo always protects your working privacy, since you can enable or disable remote access at any time.
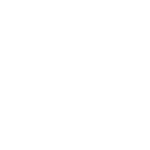
User interface language
The software is available in more than ten languages. The in-house technical department always installs the program with texts in the language of the customer, with the option of changing to English or Italian.
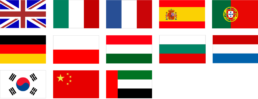
Effective integrationand communication
A fundamental prerogative of Panizzolo plants is the excellent interconnection and collaboration between the systems, especially if your objective is having an Industry 4.0 plant.
Therefore the Panizzolo technical department uses OPC UA protocol, to speed up and simplify communication bridges between different platforms and systems. Information is exchanged simply and safely, without developing complicated interconnection software.
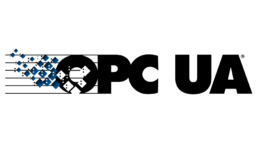
New approachesfor your business
Predictive maintenance
Starting from the customer’s business model, it is possible to perfect and customise the entire processing cycle. Predictive maintenance is a tangible example of how activity monitoring can avoid unnecessary and undesirable machine downtime. By monitoring the standard parameters, Panizzolo’s software signals, in real time, any significant variations in the areas subject to wear and high stress. The customer can thereby take preventive action, saving time and costly repairs.
Performance improvement
Many customers process types of scrap with a high concentration of inerts. The main objective of their business therefore becomes the correct setting of the plant to get the maximum value of the metals contained and to limit management costs. Investing in new recycling technologies and monitoring the workflow allows you to customise the treatment cycle to achieve the right balance between costs and profits.
Towards the futureof the sector
It’s good to keep up-to-date on a market always on the move.
Follow the news in the sector and the Panizzolo columns.