Kraken: the new Panizzolo pre-shredder
Kraken: the new Panizzolo pre-shredder
Performance, reliability and safety: Kraken is Panizzolo's new solution for the pre-shredding of high-impact scrap. Let's find out together how this new project started.
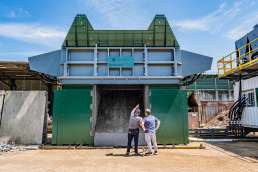
In a recycling sector increasingly characterized by complex flows and growing material volumes, it is essential to adopt solutions that guarantee reliable performance and operational continuity from the early stages of processing. It is precisely from this need that Kraken was developed, the series of industrial pre-shredders Panizzolo dedicated to the volumetric reduction of the most challenging scrap. The series debuts with the PSH 2300 model and will soon be expanded with other versions created for different production capacities and plant engineering requirements.
In this interview, Mauro Panizzolo, Owner and Sales Manager, gives us a closer look at the new project, exploring its strengths, challenges, and strategic objectives. But before getting into the heart of the article, here’s a short video in which Mattia Molena, Marketing Manager, introduces the Kraken series, illustrating its main advantages and application context.

Kraken represents an important innovation in your range. What are the design premises of this new series?
The Kraken series was born from a double need: on the one hand to complete our offer with a dedicated pre-shredding solution that can be integrated with Mega hammer mills and matched to their performance; on the other hand, we want to meet the increasing demand from our customers: robust technology that ensures effective volume reduction and consistent flow to the next stages of the line. With the introduction of the new series, we expand our capacity to follow the entire process, from pre-shredding to refining. It is a solution that further strengthens the value of our approach: offering not only machinery, but an integrated technological system, built on concrete challenges and needs.
What materials can the Kraken series handle?
The pre-shredder was developed for the processing of high-impact scrap metal. Its robust structure, the 630-kW motor and a total weight of 95 tons allow to manage a wide range of materials: vehicles and car bales also complete with engine and mechanical parts, aluminium profiles, mixed ferrous scrap and bulky material. It is designed for those who work in high-capacity plants, where there is no room for machine downtime.
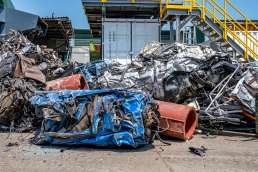
One of the most interesting aspects are the gear shafts. What differentiates them?
Behind the performance of the Kraken series is very in-depth interior design work, starting right from the gear shafts. We studied a specific geometry and configuration to obtain precise and controlled tearing, capable of reducing the material in a single pass. This ensures a regular flow towards the mill, maximizing the energy efficiency and minimizing mechanical stress on downstream machines.
Now let’s talk about maintenance and durability. How did you address these aspects?
Durability and the simplicity of intervention. These were two key points in the design, in line with our construction philosophy. The pre-shredder is equipped with a shaft quick release system, which allows the replacement of components subject to wear in reduced times. The bearing supports are also designed to protect mechanical parts from dust and contaminants, ensuring continuity even in harsh environments.
Added to all this is a compact and functional configuration: the electrical panel and hydraulic power unit are placed in dedicated containers, a choice that simplifies transport, installation and start-up, with maximum logistical flexibility also for existing systems.
Power, control and operational continuity. Kraken is Panizzolo's answer to the most complex challenges of industrial pre-shredding.
And in terms of security, how does the Kraken pre-shredder perform?
We developed the new series with particular attention to safety in real-world contexts of use. The pre-shredder is capable of processing potentially critical components, such as cylinders or tanks, opening them and removing any residual gas or flammable liquids. This is a fundamental function, especially when dealing with mixed scrap where the content of the input is not always predictable. In this way you reduce the risk of explosions, failures or damage to downstream machinery, helping to make the entire plant safer and more stable.
Construction quality has always been an essential aspect of the Panizzolo approach. How does this translate to the Kraken project?
In this case too we have rigorously applied our Quality Policy: certified metalwork, reinforced welding and selected components from internationally recognized Italian and Northern European suppliers.
A concrete example are the planetary gearboxes, a top-of-the-range solution chosen for their ability to withstand extreme loads and work continuously even in critical operating conditions. This approach, oriented towards maximum quality, translates into a reliable solution, durable and high-performance, with optimised operating costs and a return on investment that consolidates in the long term.
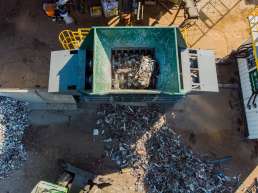
Control software plays an important role in managing manufacturing processes. How was it designed?
The Kraken series control system is intelligent and flexible. Operators can choose from preset recipes or create custom configurations depending on the material. This makes it possible to optimize consumption, reduce mechanical stress and better manage the production cycle, even in the most dynamic contexts.
The Kraken pre-shredder is part of a major project in the United Arab Emirates. What is this project about?
The new solution is one of the key elements of the system we are building for Emirates Global Aluminum (EGA), one of the world’s leading producers of aluminium. We are talking about a large-scale project: it will be the largest plant of its kind in the United Arab Emirates, with a processing capacity of up to 170,000 tons of scrap per year. It is a strategic stage in the roadmap of decarbonization by EGA, designed to produce high-quality, low-emission secondary aluminium. For us it is much more than a simple supply: it is a technological collaboration at the highest level which consolidates our role as strategic partner for the development of plants that meet global environmental challenges.
Want to know more about Kraken pre-shredders? Contact us for more information.
Aluminium recycling in relation to innovation and sustainability
Aluminium recycling in relation to innovation and sustainability
Aluminium recycling drives the transition to a more sustainable industry. In this article we discover how Panizzolo technologies meet the needs of international players, combining innovation, efficiency and resource valorisation.
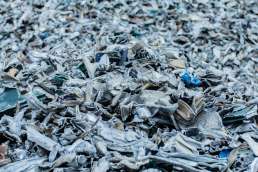
In a world racing towards ever more ambitious sustainability goals, aluminium recycling has become a strategic asset for the future of the industry, thanks to its properties of lightness, strength and, above all, infinite recyclability.
One of the most significant benefits concerns energy savings: according to the International Aluminium Institute, recycling aluminium saves up to 95% of energy compared to production from virgin raw material. It is also estimated that the recycling of post-consumer scrap avoids the production of about 20 million tonnes of primary aluminium each year, contributing to the reduction of about 300 million tonnes of CO₂.
It is no coincidence that aluminium is considered one of the strategic materials to achieve the targets set by the European Green Deal, as well as the decarbonisation goals of the world’s major economies. The focus is increasingly shifting towards secondary metals, key resources to fuel production processes while minimising emissions.
Recycling as an economic lever
Aluminium recycling is not only a virtuous choice from an environmental point of view, but represents a concrete opportunity for growth and competitiveness for companies. Using quality secondary raw materials means significantly lowering energy and operating costs compared to the extraction and processing of bauxite. Furthermore, by reducing dependence on virgin raw materials, companies become less exposed to global price fluctuations and geopolitical risks. The result is more sustainable, resilient and cost-effective production, in line with the expectations of an increasingly ESG-conscious market.
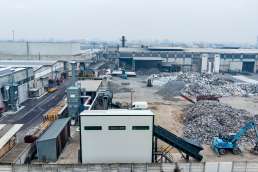
Efficient technologies for the future of recycling
In this scenario, the main challenge is to increase investments in the technological innovation of recycling processes. It is with this in mind that we design our plants, developing tailor-made solutions that maximise the recovery of secondary raw materials, optimise costs and increase process profitability. Every day we speak with different production companies, each with specific needs and complexities to deal with. This direct experience guides our design approach, turning customers’ operational challenges into strengths that make each system efficient, flexible and result-oriented.
PROCESSING FLEXIBILITY
Our plants are designed to handle a wide range of aluminium scrap, from window and door profiles from demolition work to car casings, and even aluminium packs and mixed casings. The integration of patented components, such as the interchangeable cradle, allows our solutions to easily adapt to different markets, companies and application contexts.
MODULAR AND SCALABLE SOLUTIONS
Thanks to a customised approach, our systems can meet the needs of companies of all sizes, all of which share a quest for quality, performance and profitability. Each plant is designed to be modular and grow with the company, following the evolution of production needs. A real advantage for optimising initial costs and planning future investments with greater flexibility.
HIGH PRODUCTIVITY
A key element of Panizzolo’s aluminium plants are the Mega and Flex series hammer mills, designed to offer superior performance in terms of productivity and efficiency. The Mega series, for example, can process up to 2.2 times the amount of material compared to the market standard, ensuring operational continuity and resistance to even the most demanding workloads.
OUTPUT QUALITY
Our systems integrate grinding, separation and refining technologies to achieve total recovery of secondary raw materials, with high purity output suitable for direct remelting and reintroduction into the economic cycle. This translates into higher value per tonne and the ability to satisfy even the most demanding segments of the metal industry.
Advanced and flexible solutions for End-of-Waste treatment of aluminium.
Panizzolo and EGA, a partnership for the largest aluminium recycling plant in the Emirates
The drive towards more sustainable production processes is redefining the aluminium industry’s strategies and more and more companies are investing in advanced equipment to create value in a sustainable way. It is in this scenario that the collaboration with Emirates Global Aluminium (EGA) fits in.
EGA, one of the world’s largest aluminium producers, has started construction of the largest aluminium recycling plant in the United Arab Emirates, with a planned production capacity of 170,000 tonnes per year. An initiative that represents a fundamental step in the group’s decarbonisation strategy and a clear signal of transition towards a circular economy.
Our technology is at the heart of this strategic project: from processing solutions to the definition of flow logic, integration between machines and the overall organisation of the production cycle. The result will help ensure an efficient recycling process capable of producing high-quality, low-carbon aluminium, marketed by EGA under the RevivAL brand.
Underlining the importance of the project were the words of Abdulnasser Bin Kalban, CEO of EGA:
“Recycling is a major growth opportunity for our industry and for EGA. With the construction of this plant, we have taken decisive steps to develop a global recycling business. The facility will allow us to expand our low-emission metal portfolio for local and international customers, representing a new milestone for the ‘Make it in the Emirates’ programme.”
EGA’s vision aligns perfectly with our mission and future perspective: to offer solutions that innovate recovery processes, making them more efficient and profitable. In this way, we support companies on their path to sustainable growth, helping to generate lasting value.
In the coming months we will be going into more detail on this project, which confirms our commitment to designing solutions geared towards the ecological transition.
Would you like to learn more about our aluminium recovery plant or do you have other processing needs to examine? Contact us for more information.
Why choose Panizzolo mobile hammer mills
Why choose Panizzolo mobile hammer mills
From logistical convenience to operational versatility: all the reasons to choose the Flex Mobile series
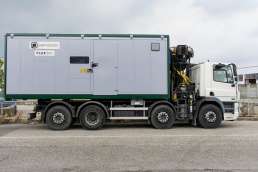
In an industrial context increasingly oriented towards speed and process optimisation, the scrap metal recycling sector requires solutions that combine operational flexibility, logistical efficiency and production continuity. These are no longer mere advantages, but real conditions for remaining competitive in the long term.
The Flex Mobile hammer mill was designed precisely to meet these needs. It was the first Panizzolo machine, developed even before the stationary models: a unique solution that paved the way for our current range of metal grinding and processing equipment.
From the outset, the series was designed to combine performance and maximum flexibility. Today, years later, it continues to be a strategic solution for companies looking for a compact, reliable and ready-to-use machine in any operational context. Originally designed for the Italian market, the Flex Mobile series has been able to demonstrate its full potential over time, establishing itself on the international scene as well, thanks to a design approach focused on simplicity and process flexibility.
A compact, efficient and flexible solution for scrap metal processing.
Logistics management and agile configuration
Designed as a turnkey, ready-to-use solution, the Flex Mobile series offers the best in convenience and speed of operation. Thanks to its configuration, transport and installation are extremely easy, even in settings with limited space. The compact design avoids oversized transport by road, simplifying logistics and reducing costs, while the special frame facilitates loading and unloading. Installation is equally simple and quick: the machines are supplied pre-assembled, mounted on roll-off boxes and, in the case of the Flex Mobile 1000, with integrated pistons that facilitate lifting and positioning, guaranteeing full plant operation in just a few steps.
Flexibility in scrap handling
What makes Flex mobile mills extremely competitive is their operational flexibility. Thanks to the patented cradle, it is possible to change processing configuration in less than twenty minutes, quickly adapting the system to the type of material to be processed or the desired size of the output product. From small transformers to electric motors, from WEEE scrap to shredded aluminium and tin cans, to mixed iron-plastic materials: the Flex Mobile series allows a wide variety of scrap to be processed, meeting the needs of companies operating in different sectors and looking for uncompromising versatility.
Energy efficiency
The Flex Mobile series includes models with powers from 90 kW to 315 kW, capable of handling between 3.5 and 15 tonnes/hour depending on the configuration. A central aspect is energy efficiency: each component is designed to maximise the ratio of energy consumption to productivity. According to an analysis based on public market data, the Flex series provides energy savings of between 22% and 62%. This has a direct impact on reducing operating costs and contributes to making the treatment process more environmentally sustainable as well.
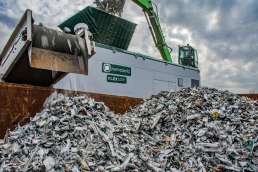
Easy maintenance
An efficient treatment plant cannot do without agile maintenance. In this respect too, Panizzolo’s mobile mills are an optimal solution. The machine is designed to facilitate the inspection, greasing and replacement of components subject to wear. Thanks to full access to the grinding chamber, the cradle, rotor, grids, hammers and armours can be easily serviced. All operations are simple and intuitive reducing the number of operators involved and without the need for special equipment or advanced technical skills. This approach results in leaner plant management, optimising overall efficiency.
Reducing noise emissions
A further strength of the Flex Mobile series is the presence of sound-absorbing panels integrated in the external structure. These are specific, water-repellent and weather-resistant materials which guarantee a significant reduction in noise emissions during operation. This feature makes the Panizzolo mobile mill ideal for production contexts where noise management and compliance with environmental regulations are crucial. But not only that. Noise reduction helps to create a more comfortable environment for operators, reducing the risks of exposure to high noise levels, in full compliance with occupational health and safety regulations.
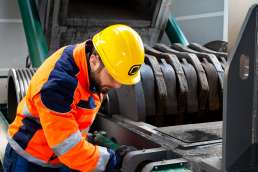
Quality-oriented design approach
In line with our high-quality standards, the mobile mills are built for longevity and high performance. Wear is concentrated only on easily replaceable components, such as hammers, grids and armours, made from special steels and high-grade castings. The high quality of the materials – from the framework to the welds – helps to preserve the integrity of the mill even when crushing the heaviest scrap.
Rotors and hammers respond to the same construction logic: the rotors are designed to efficiently absorb mechanical stresses, while the hammers, with free 360° rotation, guarantee optimal impact and efficient crushing, reducing the risk of breakage and ensuring continuity of performance.
These measures reflect the design philosophy that unites all our solutions, which is oriented towards a precise objective: to provide reliable systems, designed to last and capable of adding value to the investment in the long term.
Would you like to know more? Contact us for more information.
Panizzolo's solutions for WEEE recovery
Panizzolo's solutions for WEEE recovery
Innovation, flexibility and efficiency to maximise WEEE recovery
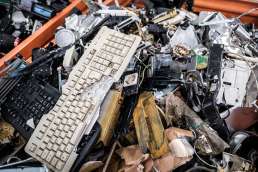
The treatment of Waste Electrical and Electronic Equipment (WEEE) is one of the most pressing challenges for the recycling industry. According to the Global E-waste Monitor, more than 62 million tonnes of e-waste will be generated globally in 2022. To give an idea, the volume of WEEE produced would be enough to fill 1.55 million 40-tonne trucks, an unbroken line of vehicles that could circle the entire earth’s equator.
Another relevant figure concerns the recycling rate: only 22.2% of WEEE is treated and recovered correctly, leaving tonnes of valuable materials unused. This leads not only to a significant environmental impact, but also to an estimated economic loss of more than 62 billion USD per year, highlighting how much the potential of these materials is still underestimated.
Every discarded electronic device contains precious metals such as copper, aluminium, steel, iron and other reusable materials. Recovering them efficiently is key to reducing dependence on virgin resources, limiting environmental consequences and maximising the value of waste.
At Panizzolo, we turn this challenge into an opportunity. Our grinding, separation and refining plants process large household appliances (category R2), small household appliances and consumer electronics (category R4), recovering high-quality iron, copper, aluminium and steel granules, ensuring an efficient, sustainable and value-oriented process.
Advanced technology and tailored solutions to maximise the recovery of WEEE and enhance every step of the process.
WEEE recovery, step by step
To maximise the valorisation of WEEE, we have developed a processing cycle that integrates the grinding, separation and refining phases, with an End-of-Waste approach. Specifically, the plants apply only mechanical and in-line treatments, with productivity ranging from 3 to 20 ton/h.
Grinding
A key element of the process is the grinding phase, entrusted to the Mega and Flex series hammer mills, designed to offer superior performance in terms of productivity, energy efficiency and adaptability to different types of WEEE. Thanks to their solid construction and patented components, Panizzolo mills guarantee optimal volumetric reduction, facilitating the separation of ferrous and non-ferrous components.
Separation
Subsequently, the material undergoes a sorting process, which uses advanced technology to achieve extremely precise separation of the different metal and plastic fractions. This system ensures a high level of purity of the recovered materials, increasing their quality and value.
Refining
The refining stage completes the WEEE treatment cycle and provides a very high quality output, obtaining only metal granules, classifiable as secondary raw material, which can be sold directly to foundries.

Turnkey solutions for efficient recycling
Our aim is to offer much more than just machinery: we develop complete, customisable plants designed to ensure efficient and profitable recycling. Turnkey solutions combine innovation, flexibility and user-friendliness to optimise every step of the process, improving operational efficiency and reducing running costs. Our range of plants is highly modular, allowing companies to adapt and expand their production capacities according to market dynamics, even in view of new business opportunities.
Further added value is the synergy between design, installation and assistance. From initial consultation to installation, from training to after-sales service, we offer our customers all-round support, accompanying them on a path of long-term technological and production growth.
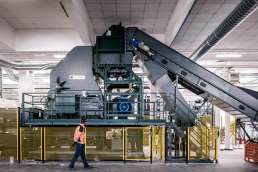
Sogliano Ambiente: a winning partnership
The collaboration with Sogliano Ambiente, an Emilia-based company that has been involved in waste disposal and treatment for more than 25 years, is a concrete example of the Panizzolo approach. From the beginning, the company needed to find a partner that could provide a tailored solution for WEEE treatment, capable of evolving over time with new implementations. The installed system consists of two main lines. The first, dedicated to volumetric reduction, includes a hydraulic opener, designed to perform manual sorting and prepare the material for the next step. The second line focuses on the grinding and separation of metals, thanks to a Flex 1000 hammer mill flanked by two advanced separation systems, which enable the end-of-waste cycle of ferrous and non-ferrous metals.
Today, the collaboration continues to evolve. Sogliano Ambiente chose to expand its plant by integrating new Panizzolo sorting islands, with the aim of further improving the quality of recovered materials and increasing the value of the final product.
Advanced training
In an ever-changing industry, investing in training is essential to sustaining business growth. That is why, through the Panizzolo Recycling Academy, we offer our customers a programme of specialised courses that enable them to acquire all the necessary skills for optimal machinery management, from operational to organisational. Thanks to an approach based on best practices and strategies applicable to the work environment, training guarantees concrete results: from optimising the energy efficiency of plants, to improving productivity, to promoting a more flexible and proactive operational approach. At the end of the course, the skills acquired in metal treatment and recovery are recognised with an official certificate, confirming the completed training.
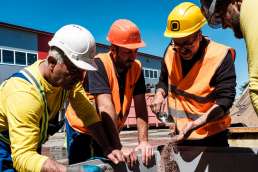
New strategic directions
Innovation is at the heart of our strategy and the engine that drives every project. This year, investments in Research and Development are focused on expanding the product range, with the introduction of new solutions, targeted technology upgrades and an increase in accessories to further improve plant performance. The push for innovation goes hand in hand with an international expansion strategy, increasingly oriented towards non-EU markets. With this in mind, we are strengthening our sales network and reinforcing our presence in key industrial areas, offering state-of-the-art solutions to meet the new challenges of the global market.
This strategic vision is also reflected in the choices related to participating in major industry events. While recognising the importance of Ecomondo, which over the years has represented an important opportunity for discussion and growth, our path this year leads us to take new directions, focusing our energies on international markets and strategic development projects. In this context, we will be involved in a number of key global events in 2025, including Residuos Expo Mexico, E-Waste World, BIR and Aluminium USA, to name a few. These events will allow us to strengthen our presence in non-EU markets, consolidate strategic relationships and bring our solutions into new contexts.
In the coming months, we will unveil more details about new technologies and upcoming projects, confirming our commitment to forward-looking solutions.
Would you like to receive more information? Contact us to learn more.
4 factors to consider when choosing a recycling system
4 factors to consider when choosing a recycling system
What aspects to evaluate when choosing a recycling system? Discover the 4 decisive factors that guarantee long-term efficiency and results.
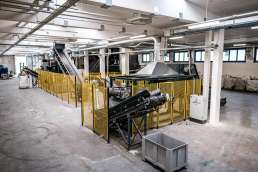
The choice of a recycling system is a strategic decision that can determine the success of a company. It is a significant investment, which must ensure efficiency, productivity and sustainability in the long run. Therefore, the process can be complex and cannot be left to chance: precise evaluations of technical, logistical and economic aspects are required.
At Panizzolo Recycling Systems we are familiar with this complexity. Since 1946, our experience gained first as tradesmen and then as system designers has allowed us to get to know the dynamics of the industry and experience first-hand the challenges that companies face on a daily basis. A key moment in our journey was the development of the Piove di Sacco system in the 1980s and 1990s. Equipped with 250 kW hammer mills, this system was a real revolution for us: thanks to low energy consumption and high productivity, we were one of the first in Italy to prove that high performance and optimised consumption can coexist.
Since then, our pragmatic and innovative approach has evolved without pause, leading us in the 2000s to the marketing of complete scrap processing systems internationally. Today, our offer is comprehensive, with flexible solutions capable of adapting to an ever-changing industry. It is this know-how, gained in the field, that has taught us which four factors are essential to consider when choosing a recycling system.
More than 75 years of experience and unique know-how: our recycling systems offer high performance, energy efficiency and customised solutions for every treatment-related need.
1. Logistics: organising space to maximise efficiency
The logistics aspect is often underestimated in system design, yet it is one of the main factors influencing productivity, safety and operating costs. Well-organised logistics ensure a smooth and uninterrupted workflow, avoiding dead spots and minimising downtime. Each system must be thought of as a dynamic organism, in which the available space must not simply be filled, but strategically enhanced.
At Panizzolo, we always start from the customer’s operational reality: we analyse the initial storage, material handling routes, loading and unloading points, and the areas dedicated to the different processing stages. Our standard systems are not rigid, but designed to be adaptable. Together with the customer, we study the best solutions to optimise every available square metre, without imposing predefined configurations. In this way, space is utilised optimally, increasing overall productivity.
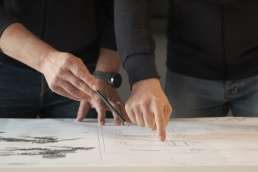
2. Energy consumption: a double challenge
Energy efficiency has become a crucial challenge for recycling companies, especially in Europe, where rising energy costs and increasingly stringent regulations impose high standards in terms of sustainability. In this context, remaining competitive means finding the right balance between output quality and consumption optimisation, minimising inefficiencies and reducing operating costs.
Panizzolo systems perfectly meet this need, thanks to innovative technologies that balance power, quality and consumption. Our hammer mills, for example, are equipped with smart control systems to monitor consumption, avoiding drops or overloads. From an energy-saving perspective, our solutions are designed to reduce waste and optimise performance. The star among them is the Mega Series, capable of achieving a productivity of 35 ton/h and energy savings of 57% to 76% compared to other models with similar motorisation.
While, in Europe, efficiency is a necessity imposed by the market, in other parts of the world the cost of energy is generally lower. In these contexts, the priority is not so much to reduce consumption as to ensure a quality of output that meets export standards. Thanks to the flexibility of our systems, we are able to meet both requirements: reducing consumption where necessary and ensuring consistent quality for the marketing of processed materials.
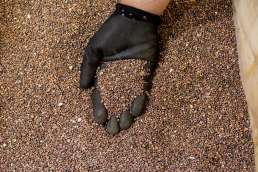
3. Quality: a long-term investment
The quality of a recycling system is not limited to the mechanical components, but is directly reflected in the performance and quality of the final output. Opting for low-cost solutions may seem advantageous at first, but it carries significant risks: frequent breakdowns, more costly maintenance work and a quality of treated material that does not meet the standards required by the market. The way we see it, quality is not a cost, but rather a strategic investment for the future. That is why we design our systems in-house, taking care of every detail and integrating advanced technologies from international brands recognised as the best in the industry for quality and reliability.
It is also crucial to devote the right resources to each step of the treatment cycle. Grinding, for example, which is often undervalued in favour of separation systems, plays a crucial role in preparing the material for the subsequent steps. Precise and uniform volumetric reduction simplifies the work of separation systems, improving efficiency and contributing to a quality-compliant end product. With this in mind, Panizzolo hammer mills guarantee optimum size, ensuring maximum synergy between grinding and separation.
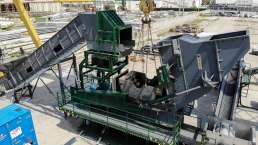
4. Flexibility: the key to the future of the sector
The recycling sector is characterised by constant evolution: new regulations, complex waste and changing market dynamics require companies to be ready to change fast. Therefore, the choice of a recycling system, also given its scale, cannot be limited to meeting current needs, but must be designed to support the company’s future growth. A system that meets production needs perfectly today could be obsolete in a few years if not designed with a long-term vision.
With this in mind, we develop modular and scalable systems that evolve with the customer’s business. Our interchangeable cradle, for example, allows adaptation to different types of scrap metal, while our broad portfolio of solutions and consultative approach guarantee constant support, even years later. With the possibility to integrate new modules and upgrades according to market needs, the system becomes a strategic lever to compete, innovate and grow over time.