Making the best use of car body metals: the Pollini Group’s new recycling system
With more than 40 years of activity in the car dismantling industry, Pollini Group consists of 250 employees, a production area of about 45,000 square metres and as many as 6 locations in Northern Italy. Owned by the Pollini family for no less than three generations, the Group specialises in the recycling of end-of-life vehicles, maximising component recovery thanks to the best technologies available on the market.
Precisely with a view to enhancing its recycling activities, the Pollini Group recently installed and started up a new system dedicated to the treatment of car bodywork, choosing the Panizzolo Recycling Systems Mega 1100 series hammermill for ferrous metals and End-of-Waste reclamation. We talk more about this with Matteo and Giacomo Pollini, who tell us the story of their company, their vision for the future and why they decided to install this new recycling system.
Good morning Matteo and Giacomo, can you tell us the story of Pollini Group and how it carries out its ELV recycling business?
Matteo Pollini: Our companies were founded by Lorenzo Pollini, our grandfather, some 40 years ago. Later the management passed to our parents and then to us, the third generation of this family business. Today, Giacomo Pollini presides over Pollini Lorenzo e figli while I – Matteo – manage Pollini Srl. In total, we have about 250 employees in six locations: Bedizzole, Brescia Centre, Brescia Fornaci, Capriolo, San Martino d’Argine and – the latest acquisition – Busto Arsizio.
Pollini Srl deals with scrap disposal and recycling thanks to its dedicated scrap treatment plant. Of the input material, 80% comes from the waste produced by Pollini Lorenzo e figli and 20% from externally purchased material. In our processes we use machinery such as industrial loaders, presses, shears, pre-grinders and, last but not least, the newly installed and commissioned Panizzolo Mega 1100 series hammermill.
The processing steps are different depending on the type of vehicle: for all of them, the cycle starts with a selection of parts, after which the smaller vehicles are immediately pressed while the others are pre-ground and fed into the new hammermill. Our aim is to recycle and recover as much material as possible. Currently, the metal output we get from the various treatment plants we resell to other companies or directly to steel mills, depending of course on the grades we get.
Giacomo Pollini: Pollini Lorenzo e figli deals in car dismantling. We are authorised to dismantle petrol, diesel, LPG, natural gas and electric vehicles. We purchase incoming vehicles from dealerships and workshops, from depot tenders and companies such as FCA – from which we take back production rejects and prototypes – and from private customers. The inflow thus reaches around 20/25,000 vehicles per year. We have also recently expanded our pick-up service for buses of all sizes and lorries of all kinds.
The demolition process involves the reclamation, dismantling – an almost entirely manual process – and evaluation of individual parts. The rejects are sent to the grinding plants while the parts in good condition follow a meticulous process of quality control, registration and cataloguing, and are then stored in our warehouses. These in fact boast around 350,000 items catalogued and ready for resale, and are divided into manual picking areas and high-density vertical automated warehouses designed for quick access, space-saving and goods preservation.
Through our physical shops and e-commerce, we sell spare parts to workshops, body shops and private customers throughout Italy. In particular, e-commerce, the development of which had already been planned for several years, was quickly made operational at the beginning of 2021 to cope with the restrictions caused by COVID-19. The online market is growing steadily, now covering about 10 per cent of parts sales, yet the public and companies still prefer our physical shops (covering about 50 per cent) and telephone sales (covering the remaining 40 per cent).
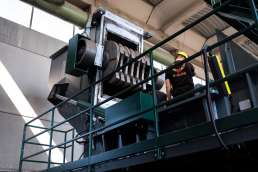
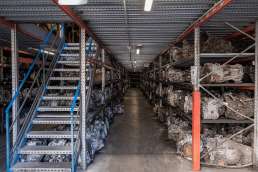
You use very special auxiliary technologies in your machining processes. Can you describe them for us?
Matteo Pollini: Yes, that is true. Thanks to our in-house workshop, we make prototypes of technologies that can facilitate certain tasks. In the case of Pollini srl, we have designed and built a vice to position the material that allows us to rotate and move the vehicle at will; in this way we can more easily remove certain materials such as the windscreen, the bumpers and the engine.
Giacomo Pollini: At Pollini Lorenzo e figli, we have also used our workshop to create a new accessory tool: a rotating platform that allows the operator to dismantle one vehicle after another, minimising downtime due to moving and positioning cars, and increasing the safety of our workers within the production area.
Your last treatment step consists in grinding the bodywork. Why did you choose Panizzolo technology to best use this scrap?
Matteo Pollini: As already mentioned at the outset, almost all of the scrap processed by Pollini srl comes from what could not be recovered within the other company branch. Among these, the material par excellence is the bodywork of end-of-life vehicles, on which we perform the final treatment stages. Until a few years ago, after a volumetric reduction of the vehicle, we operated this process with a single-shaft shredder which, however, could not meet our recovery quality requirements.
Historically, the company has always been at the forefront of technological investments to keep us competitive in the market. This is why we decided to discontinue the old machinery, preferring to opt for a hammermill that would certainly allow us to obtain the quality of ferrous and metallic proler that we are looking for.
We had already known Panizzolo for several years, having been historical suppliers of scrap metal for its treatment plant, and in discussions with Fabrizio Scussolin – Panizzolo Recycling Systems’ sales manager for Italy – we had an excellent constructive discussion on which machine model could make the best use of our type of scrap from end-of-life vehicles. We therefore almost immediately turned to the Mega 1100 hammermill model for several reasons: the excellent price/performance ratio, the hourly productivity, the excellent energy consumption, and above all the ease and simplicity of maintenance. In addition to this, we really liked the possibility of having a flexible machine, thanks to its patented interchangeable cradle, allowing us in the near future to expand the range of scrap to be processed with this machine.
The Panizzolo Mega 1100 hammermill was supplemented with separation systems that we already had in house and from the previous system. We are currently finalising tests to refine the machine setting, but we can say that we are already getting good results.
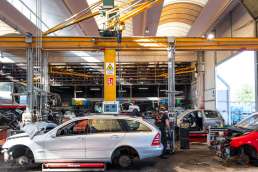
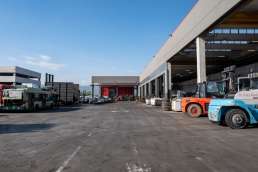
What are your goals and what do you expect from the market?
Matteo Pollini: Pollini srl ‘s main objective is to refine its treatment cycles, with a view to optimising metal recovery and reclamation. In recent years, this vision has led to several certifications such as UNI EN ISO 9001, UNI EN ISO 14001 and UNI EN ISO 45001.
We will always try to implement and refine our capabilities and technologies, so that we are always in step with changes in the market and its quality requirements. With this in mind, the new Panizzolo Mega 1100 hammermill will be the plus that will also allow us to achieve these goals and close the circular economy within the Pollini Group.
Giacomo Pollini: The scrapping sector has always been very volatile and tied to the production market, a fact that will most likely not change in the near future either. What will change, however, will be the processing methods in line with new technologies in our industry and the advent of electric vehicles. Even though we only handle about ten a month at the moment and they are mostly prototypes, we need to structure ourselves quickly to ensure the handling of this new type of waste. Electric vehicle recovery will be the challenge of the next decade and Pollini Lorenzo e figli is already starting to move in this direction, with the same professionalism and seriousness that has distinguished it for more than 40 years.
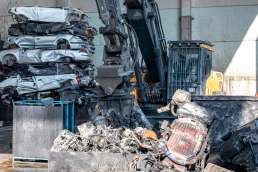
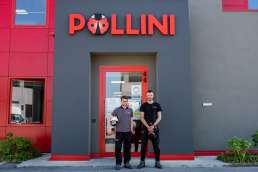