Panizzolo Recycling Systems software: how does it contribute to profitability in scrap treatment?
Panizzolo Recycling Systems integrates, in parallel with the mechanical design, the internal development of a specific software for the control and management of its recycling solutions. Why has the company structured such a specialized activity over the years?On the occasion of the recent start-up of the Compact Refining Plant, we asked this question directly to Andrea Simoni who, alongside the manager Denis Zanin, has programmed the operator interface of the recycling plant.
Hi Andrea. What is the Panizzolo software and why is it developed internally?
The software development was based on our direct experience in the treatment of metal scrap. The operator interface takes place via touchscreen and therefore we have designed simple screens of the entire treatment cycle, with an immediate understanding of monitoring and adjustments also in real time.
Owning the software and, in parallel, also the wiring diagram is essential for us. Technology is always constantly updated and external consultants could have slowed down the company’s research and development. Otherwise we can quickly install upgrades and latest generation technologies for the benefit of productivity, security and logical management. We also distinguish our attention in the translation of the entire operator interface, a necessary element to further simplify its use.
How do you go about structuring the software?
Basically, the software has a logic common to all Panizzolo recycling machines while, for more complex waste treatment plants, it includes more specific additional sections. Going into detail we find two levels of parameters. On the one hand we have the settings for essential operating safety and logic. This includes, for example, the start-up and shutdown phases where, especially in the refining plant, the electricity must be optimized and the flow of material must always be constant.
Unlike the second level, the parameters can be freely set, both during the testing phase and at a later time by the customer. The most important certainly concern the hammer mill but we also allow you to interact with other components. Specific sensors record the trend in real time, allowing the software to understand if the mill works correctly or if it must intervene to restore production balance. The parameters are always editable, even in real time, and are located in a special section called “Recipes”.
What is the operating logic of this section?
In a few words, we confirm what distinguishes Panizzolo recycling machinery: quality of the outputs and flexibility of treatment. In our experience, we know that scrap, in addition to diversifying into categories, is never homogeneous in composition. A concept as simple as it is fundamental. For this reason we have developed the “Recipes” section.
The customer clearly and intuitively displays the fundamental parameters, personalizes the types of treatment and can also make changes during processing.
I try to explain better. It happens that the need to work or test other types of material emerges in a company. Instead of changing the parameters used for daily processing, it is possible to select a new recipe and set completely new data. Once confirmed, these parameters can be unique with personalized names.
As already mentioned, the refusal at the entrance is never completely homogeneous. Through the recipes we allow to regulate loading and flows, so that mill and separation systems can optimize all treatment steps. On this topic, during the training of the Compact Refine Plant, we clarified the meaning of "processing optimization" for Panizzolo.
With our software we don’t just want to avoid overloading the machinery but we want to allow continuous and balanced processing, which is able to bring benefit to final quality, hourly productivity and component integrity.
Does training therefore play a fundamental role?
Absolutely. During the testing phase, we optimize the first recipe together with the customer and his operators. We are already able to load our predefined treatment parameters, however once in the field and with the actual scrap we proceed to confirm these calibrations. We follow a precise procedure, bringing the production to a steady state and explaining every single step to the operators: what parameters to touch and how they influence, what we recommend keeping an eye on, how to intervene according to the situations and much more. Our goal is to provide a solid starting point and allow customers to build their own experience. With the testing of the Compact Refine Plant we pay more attention to these phases, as each component is designed to bring a certain production benefit.
In addition to your experience, how does the software help you in training?
The monitoring graphs allow you to better clarify the grinding of the hammer mill. If the treatment cycle is a continuous start and stop, at the end of the day or at the end of the month, the software will highlight the accumulation of work vacuums, confirming the gap between working hours and actual production.
Always the graphs allow you to maximize productivity and at the same time avoid overloading or blocking the mill. With the training we try to pass as much information as possible to the operators. However, if the customer has specific needs, we are always present with advice and assistance in post-sales.
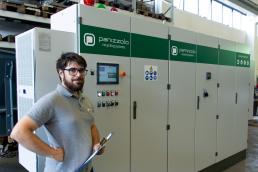
What are the benefits of Panizzolo software for maintenance?
In case of malfunctions, the software indicates the area to be checked, attaching an explanation of the problem and avoiding the operator to waste time with generic alarms. Specific warnings appear periodically for routine maintenance, the execution of which must be confirmed manually, and then remain stored in the internal memory. Being owners of both the software and the wiring diagram, we are doubly efficient on the assistance side. We have full competence of all the electronics installed, even if only trivially for a matter of spare parts, while the control panel is supplied already prepared for internet connection for remote assistance.
What improvements are you planning for the near future?
At Panizzolo Recycling Systems we care a lot about the constant electrical, electronic and software updating and therefore for this reason we have a lot of projects . Without going into too much detail, we are focusing a lot on remote assistance, much appreciated by our customers. We have recently introduced a new generation touchscreen, programming a series of updates and implementing new parameters.