Software Panizzolo Recycling Systems: in che modo contribuisce alla redditività nel trattamentodei rottami?
Panizzolo Recycling Systems integra, parallelamente alla progettazione meccanica, lo sviluppo interno di uno specifico software per il controllo e la gestione delle sue soluzioni di riciclaggio. Per quale motivo l’azienda ha strutturato negli anni un’attività tanto specializzata? In occasione del recente avviamento dell’Impianto di Raffinazione Compact, abbiamo rivolto questa domanda direttamente ad Andrea Simoni che, affiancando il responsabile Denis Zanin, ha programmato l’interfaccia operatore dell’impianto di riciclaggio.
Ciao Andrea. In cosa consiste il software Panizzolo e perché viene sviluppato internamente?
Lo sviluppo del software si è basato sulla nostra diretta esperienza nel trattamento dei rottami metallici. L’interfaccia operatore avviene tramite touchscreen e dunque abbiamo progettato semplici videate di tutto il ciclo di trattamento, con un’immediata comprensione di monitoraggi e regolazioni anche in tempo reale.
Essere proprietari del software e, parallelamente, anche dello schema elettrico per noi è indispensabile. La tecnologia è sempre in costante aggiornamento e consulenti esterni avrebbero potuto rallentare l’attività di Ricerca e Sviluppo aziendale. Diversamente possiamo rapidamente installare upgrade e tecnologie di ultima generazione a beneficio di produttività, sicurezza e gestione logica. Ci distingue inoltre la nostra attenzione nella traduzione di tutta l’interfaccia operatore, un elemento necessario per semplificarne ulteriormente l’utilizzo.
Nella strutturazione del software generalmente come procedi?
Di base il software presenta una logica comune a tutti i macchinari di riciclaggio Panizzolo mentre, per gli impianti di trattamento rifiuti più complessi, comprende sezioni aggiuntive più specifiche. Scendendo nel dettaglio troviamo due livelli di parametri. Da una parte abbiamo le regolazioni per sicurezze e logiche essenziali di funzionamento. Ne fanno parte per esempio le fasi di avviamento e spegnimento dove, specialmente nell’impianto di raffinazione, l’energia elettrica deve essere ottimizzata e il flusso di materiale deve essere sempre costante.
A differenza il secondo livello comprende parametri liberamente impostabili, sia durante la fase di collaudo sia in un secondo momento dal cliente. I più importanti sicuramente riguardano il mulino a martelli ma permettiamo anche di interagire con altri componenti. Specifici sensori registrano l’andamento in tempo reale, permettendo al software di capire se il mulino lavora correttamente o se deve intervenire per riportare equilibrio produttivo. I parametri sono sempre modificabili, anche in tempo reale, e si trovano in un’apposita sezione definita “Ricette”.
Quale è la logica di funzionamento di questa sezione?
In poche parole confermiamo ciò che maggiormente distingue i macchinari di riciclaggio Panizzolo: qualità degli output e flessibilità di trattamento. Per nostra esperienza sappiamo che il rottame, oltre a diversificarsi in categorie, non è mai omogeneo nella composizione. Un concetto tanto semplice quanto fondamentale. Per questo motivo abbiamo sviluppato la sezione “Ricette”.
Il cliente in maniera chiara ed intuitiva visualizza i parametri fondamentali, personalizza le tipologie di trattamento e può eseguire modifiche anche durante la lavorazione.
Cerco di spiegarmi meglio. Capita che in un’azienda emerga la necessità di lavorare o testare altre tipologie di materiale. Invece di modificare i parametri utilizzati per la lavorazione quotidiana, è possibile selezionare una nuova ricetta e impostare dati completamente nuovi. Una volta confermati, tali parametri potranno essere resti univoci con nomi personalizzati.
Come già detto il rifiuto in ingresso non è mai completamente omogeneo. Tramite le ricette permettiamo di regolare caricamenti e flussi, così che mulino e sistemi di separazione possano ottimizzare tutti i passaggi di trattamento. Su questo argomento, durante il training del Compact Refine Plant, abbiamo fatto chiarezza sul significato di “ottimizzazione della lavorazione” per Panizzolo.
Con il nostro software non vogliamo solo evitare il sovraccarico dei macchinari ma vogliamo permettere una lavorazione continua ed equilibrata, che sia in grado di portare beneficio a qualità finale, produttività oraria e integrità dei componenti.
L’attività di training svolge dunque un ruolo fondamentale?
Assolutamente. In fase di collaudo ottimizziamo la prima ricetta insieme al cliente e ai suoi operatori. Siamo già in grado di caricare i nostri parametri predefiniti di trattamento, tuttavia una volta sul campo e con l’effettivo rottame procediamo a confermare tali tarature. Seguiamo un preciso iter, portando in sicurezza la produzione a regime e spiegando ogni singolo step agli operatori: quali parametri toccare e come influiscono, cosa consigliamo di tenere d’occhio, come intervenire a seconda delle situazioni e molto altro ancora. Il nostro obiettivo è fornire una solida base di partenza e permettere ai clienti di costruirsi una propria esperienza. Con il collaudo del Compact Refine Plant prestiamo maggiore attenzione a queste fasi, in quanto ogni componente è progettato per apportare un determinato beneficio produttivo.
Oltre alla vostra esperienza, come vi aiuta il software nel training?
I grafici di monitoraggio permettono di chiarire maggiormente la macinazione del mulino a martelli. Se il ciclo di trattamento è un continuo start e stop, a fine giornata o a fine mese il software evidenzierà l’accumulo dei vuoti lavorativi, confermando il gap tra ore di lavoro e produzione effettiva.
Sempre i grafici permettono di massimizzare la produttività e allo stesso tempo evitare il sovraccarico o il blocco del mulino. Con il training cerchiamo di passare quante più informazioni possibili agli operatori. Tuttavia qualora il cliente abbia necessità specifiche siamo sempre presenti con consulenze ed assistenze nel post vendita.
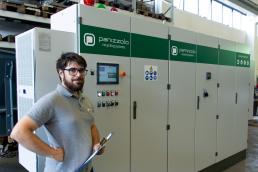
Quali benefici porta il software Panizzolo alla manutenzione?
Nel caso di malfunzionamenti il software indica la zona da controllare, allegando una spiegazione della problematica ed evitando di far perdere tempo all’operatore con allarmi generici. Periodicamente compaiono avvisi specifici per la manutenzione ordinaria, la cui esecuzione deve essere confermata manualmente, per poi rimanere archiviata nella memoria interna. Essendo proprietari sia del software che dello schema elettrico siamo doppiamente efficienti dal lato assistenziale. Abbiamo piena competenza di tutta l’elettronica installata, anche solo banalmente per una questione di ricambistica, mentre il pannello di controllo viene fornito già predisposto al collegamento internet per l’assistenza da remoto.
Quali miglioramenti avete in programma per il prossimo futuro?
In Panizzolo Recycling Systems teniamo molto al costante aggiornamento elettrico, elettronico e software e dunque per questo motivo abbiamo molto progetti in cantiere. Senza entrare troppo nel dettaglio, ci stiamo focalizzando molto sull’assistenza da remoto, molto apprezzata dai nostri clienti. Abbiamo da poco introdotto un touchscreen di nuova generazione, programmando una serie in aggiornamenti e implementando nuovi parametri.
Insieme al responsabile Denis Zanin, programmiamo le implementazioni restando ancorati ad una logica di semplicità e di immediata comprensione. Deve essere sempre il software ad adattarsi al ciclo produttivo, il cui scopo è ottimizzare e massimizzare sia le potenzialità produttive dei macchinari sia la qualità dei metalli in uscita.