Interview with Luca Pallotti, director and commercial manager of Ferrotrade
Located in Genoa with three offices, Ferrotrade actively acts throughout Liguria and in part of Northern Italy both in the collection and treatment of metal waste, providing a high quality secondary raw material in Italian foundries and steel mills.Reliability, seriousness and technological investment are the distinctive elements of this family-run company. Let's find out more about its peculiarities together with Luca Pallotti who, at the new headquarters, installed the Panizzolo Recycling Systems treatment plant with a stationary Flex 800 hammer mill.
Good morning Luca. What is the history of Ferrotrade and what role does it play in the national market?
We are a relatively young company but with a long tradition in the scrap trade sector. Together with my father Salvatore and my sister Patrizia, we founded Ferrotrade in 1998 starting with about 4-5 people and dealing mainly with ferrous and demolition scrap. Over the years we have gradually expanded the commercial network and expanded the range of waste, relying today on three production sites in the Genoa area and more than doubled staff.
As a sales manager, I have solid contacts with many Ligurian, Lombard, southern Piedmont and Northern Italy companies. We collect scrap from small artisans, from mechanical workshops, body shops, demolition cars, Ec-center and from large companies such as Ferrovie dello Stato, Autostrade per l’Italia and Ansaldo Spa.In addition to the treatment of ferrous scrap, thanks to the Flex 500 Mobile mill since 2012 we have also expanded to the enhancement of mixed aluminum. A company branch in constant expansion and which today sees a new mill and many new scrap in action.
Why did you choose to work with Panizzolo machines?
We have known Mauro Panizzolo since he dealt with car engines in his recycling plant near Padua. When we hit the market looking for a new treatment plant we visited their headquarters, where we were pleasantly surprised by the quality of the hammer mills.
Mauro's direct experience for us was a guarantee of quality and technological innovation, confirmed both in tests and then in daily use.
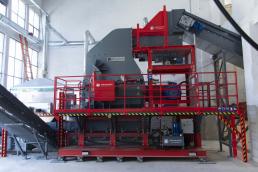
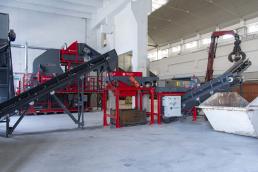
Why did you choose the Flex 500 Mobile in 2012 and what was your experience?
At the time we chose this model because it was the most versatile and compact, with a decent engine and hourly productivity. It possessed an original design, a sturdy carpentry, structured for easy transport and complete with soundproofing. In the city of Genoa, the space for us as companies is still very limited, forcing us to optimize all production and storage areas. The Panizzolo hammer mill was a choice that met our expectations also from this point of view. Another plus we found is the interchangeable cradle, allowing us in those years to have many experiences of mixed metal recycling, WEEE treatment, collection from MSW and more.
So did you find the patented interchangeable cradle very useful?
The interchangeable cradle gives Panizzolo Recycling Systems machinery an edge over other models on the market. The cradle avoids wasting time, speeds up production changeovers and makes the hammer mill a versatile machine for a wide range of processing cycles
My operators still use it a lot even in the new Flex 800 Stationary, planning certain types of grinding or refining in time. In just under an hour we can go, for example, from grinding aluminum to the treatment of WEEE.
The interchangeable cradle has allowed us, especially in this unexpected period of health crisis, to move quickly to the treatment of other more profitable materials and always producing a high quality output that can be delivered to the foundry or steel mill.
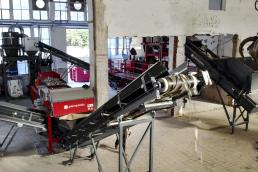
Why did you decide to switch to the Flex 800 hammer mill?
By specializing in waste treatment, year after year we have increased our purchasing pool. We mainly collect ferrous scrap, but we are also progressing well on the aluminum front, electronics from WEEE, mixed metals and separate collection from Eco-centers in the province.
In 2019 we had the opportunity to expand to a third location, activating a new storage and treatment authorization for a quantity of approximately 50 tons of waste per day. Discussing with Mauro Panizzolo we decided that the most suitable mill for our new production needs was the stationary Flex 800, with which we currently treat 5 tons / hour of mixed aluminum and whose output is subsequently enhanced with a magnetic drum, an air separator and an eddy current.
Some manufacturers claim that grinding aluminum with hammer mills is counterproductive due to the losses in dust. Given your long experience, what is your opinion?
It all depends on knowing the correct course of treatment. In this period of crisis, where many strategic sectors have reduced the purchase of raw materials, market penetration is strongly linked to the purity of the metal that a company is able to obtain.
The Panizzolo Recycling Systems hammer mill allows us to achieve an important qualitative leap in aluminum, with an economic sales value that could hardly be achieved with other machinery. To avoid unnecessary losses, we at Ferrotrade set the grids in such a way that the material is ground only strictly necessary, so much so that we currently find small quantities of aluminum powders. Moreover, if we really want to be honest, with the right commercial connections, the latter also have their own appropriate sales channel.
Why is the best direction to produce secondary raw material?
Anyone in our industry has been able to see the sudden changes in recent years. Foundries and steel mills demand higher quality every day and the market reacts accordingly, it has become increasingly difficult to market scrap that does not meet these demands.
The only solution is to invest in new treatment technologies, as we at Ferrotrade did, otherwise you risk losing the competitive advantage in both buying and selling. At the same time it is necessary that these technologies are flexible in the treatment, allowing to perform rapid production changes according to market trends.
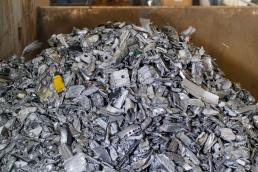
A bit like we did with the Panizzolo Recycling Systems hammer mill: today we work with mixed aluminum, but in a very short time we can switch to other metal scrap.
Do you consider that the future of the sector will go in this direction?
Absolutely, we have been investing in this direction for many years. To attest to our growth path we can boast the ISO 9001 and ISO 14001 certificates for the high quality of our production process, as well as the 333 and 715 certifications for the production of secondary raw materials. Obviously, these certificates are obtained only after considerable personal and economic investments, however today they are indispensable when you deal with many medium-large companies, both in the purchase and sale of the material.
Thanks to the Panizzolo Recycling Systems plant, we supply Italian foundries and steel mills with a product that I don’t say is the same as an ingot or billet, but it is still a high quality material ready to be melted in their furnaces. Ensuring a constant quality output is not at all simple, however the combination of our experience and that of the Panizzolo service allows us to maximize the productivity of the plant and the quality of the outputs.