INTERVIEW WITH MR. SCHUSTER
ENHANCEMENT OF THE GERMAN ALUMINIUM SCRAP WITH PANIZZOLO HAMMER MILLS
Schuster Metall-Recycling GmbH is headquartered in Wemding, Germany. Located about halfway between Munich and Frankfurt, it has worked for many years in the treatment of various types of waste, with a specialization in the aluminium profile. Mr Schuster‘s technical and engineering experience, combined with practical knowledge of the world of scrap trading, allows him to choose the correct machinery to get the most from metals and confer them directly to German foundries.
Who is Mr Schuster? What about the Company and his history?
Founded by my father and now run by me, we started fifty years ago with simple world of scrap trading. Over the years we have decided to specialize in metal treatment. We have installed recycling systems and consequently increased our presence in the German and foreign market. Today the company sells more than 3000 tons per month of second raw material that we directly deliver to the foundry. More or less the sales are distributed around 60% in Germany and 40% in European countries.
What makes us different in the German market today is the efficiency of the recycling plants we work with, the high quality output, professionalism in relationships and flexibility of treatment.
Where does your technical knowledge of treatment plants come from?
I learned on my own. Processing the material and seeing what you can do with it.
I work with lots of machines and I have to understand what I want to obtain from each machine. The most of machines that I bought are still working on my plant. My next goal is very hard, but I want to improve the output quality. In this moment it is not easy to find a good material, it depends on price. There is no scrap in market, due to car crisis.
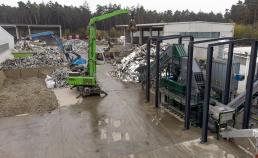
Do you think that German and Italian scrap companies are similar?
Yes, they are similar. We treat a wide range of metal scrap but we specialize in aluminium. For this reason, many times we market with foreign countries, including Italy. In general, the German market has a slightly higher metal quality than other countries.
What type of recycling plants do you work with? Where do you deliver their outputs?
In our company there are cable treatment plants, presses, shredders, separation systems and a Panizzolo Mega 1100 hammermill. For the most part the outputs produced, are supplied in national foundries and also in countries such as Italy, Austria and Poland. For example, the Panizzolo Mega 1100 hammermill mainly works with an aluminium profile, the output of which is transformed by the German foundries into raw materials mainly for the automotive market.
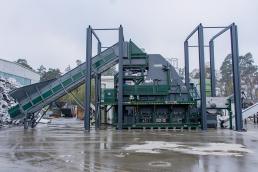
Why did you decide to use a hammermill?
Because the Mega 1100 hammermill allows us to obtain a perfect aluminum quality for direct transfer to the foundry. For example, a shredder would never allow us to achieve this goal. All European foundries, and especially German foundries, demand ever greater quality from the material they buy. There is quality and quality of aluminum. For example, Italian foundries want an aluminium quality different from ours because they have other outlet markets. However, the quality standards are growing day by day.
Why did you choose Panizzolo hammermills?
Because Panizzolo recycling solutions are simple to use, they are not huge machines and are very strong. Totally suited to my needs. The first hammermill I purchased from Panizzolo was Flex 1000 Mobile drum. It was one of the first hammermills I used, so I had to weigh the investment well. The machinery has lived up to expectations and has worked for almost ten years with an average production of about 6 tons/h. Currently from the new Mega 1100 hammermill I get an output production of 12 tons/h. I think that I will also easily reach at 15 tons/h, as it is working 70% of its potential.
What do you think of the interchangeable cradle in our hammermills?
It is an excellent idea and another factor of uniqueness that made me choose working with you.
The aluminium profile that I buy is not always the same and the cradle guarantees me flexibility and setting speed in the Mega 1100. Maintenance is simple, safe and quick, allowing to reduce all downtimes. Furthermore, in the near future it will allow me to perform fast treatment tests on other kinds of waste.
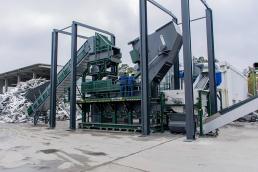
Other pluses that you found in the Panizzolo mill?
In general I like the whole construction logic. You can immediately see that the design is the result of years of direct experience in the sector. I myself have created my baggage of technical experience by operating directly. Mauro Panizzolo and I have the same vision of what is technically needed in a machine to work better. Concrete example are the hammers in special casting, born from a study in partnership with University of Padua. When I tested them I saw a radical difference in the wear and the quality of outputs.
Have there been any changes in the German scrap market in recent years? What future lies ahead in this sector in Germany?
Certainly in recent years there have been important changes, due both to internal and external factors. In Germany, the crisis in the automotive sector caused a drop in the purchase of foundries. The closure of China allows us to keep more scrap within our borders but we are experiencing a shortage in quality.
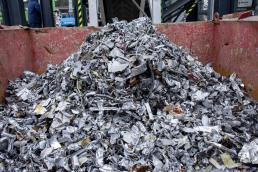
The future of the sector will focus on the treatment of scrap and the enhancement of metals.
When China reopens import, it will be only for semi-finished products and Germany is a nation that needs excellent quality raw materials for its products. It therefore makes no sense to continue marketing scrap as it is. One of our major strengths is the quality of the output metals. The combination of my technical and commercial experience and the use of Panizzolo machinery will be the winning weapon for the next few years to come.
What advice would you give to German companies that would like to install a treatment plant?
Unfortunately there are no big shortcuts. You must be clear in what you want to achieve at the end of the production process. You must always keep up with what market requires and build your own baggage of experiences, as I did. Finding a trusted technology supplier is not easy and unfortunately many pretend to be what they are not. Fortunately, I found in Panizzolo a valid partner who designs excellent machinery and which allows me to maximize the enhancement of the metals I sell.