Panizzolo Recycling Systems and the news of Ecomondo 2020
Panizzolo Recycling Systems and the news of Ecomondo 2020
The scrap market is shaken by important changes, especially accelerated by the recent COVID-19 emergency. While continuing to invest in new recycling cycles, scrap processing companies analyze operating costs much more thoroughly than in the past.We talk more about it with Matteo Turatto, Sales Director at Panizzolo Recycling Systems, clarifying how this is connected both to the consolidation of technological supplies and to the innovations that will be presented at the next edition of Ecomondo 2020 .
Good morning Matteo. How is the scrap market changing? And in what direction Panizzolo is moving ?
Compared to four or five years ago, the sector is evolving in a very clear direction: companies must make the most of metals if they do not want to lose their competitive advantage. The market requires the recovery of more complex waste, which requires ever more efficient recycling plants. For this reason, in the analysis phase, companies are more sensitive to all those qualitative aspects that give an economic return in the medium to long term. Exactly on this front Panizzolo Recycling Systems has consolidated its market positioning, with excellent response from both Italian and foreign customers.
Through which strengths the Panizzolo recycling and refining plants meet the needs of the sector?
We are chosen because we know how to offer innovative technologies, with management costs much lower than other recycling machines on the market. Today, it becomes essential for companies to know the operating costs that will result from the investment: management of the scrap treatment cycle, energy consumption, maintenance and spare parts, personnel employed and more. The low costs of the Panizzolo lines benefit the productivity of the plant, a crucial node for the economic prospects in the medium and long term. In addition to this, customers appreciate our professionalism in providing turnkey solutions and high quality in supporting the technical staff .
How have you achieved these successes?
Continually investing in Research and Development in our historic headquarters, where there are only waste treatment plants designed by Panizzolo. Here we have developed high quality flexible technologies, with very important patents in hammer mills and refining plants.
The success of our treatment solutions comes from the ability to correctly balance costs, continuous production reliability, flexibility in the fields of application and the enhancement of the outgoing fractions.
The solutions in refining plants are particularly appreciated for the innovative treatment cycle, responding to a demand that the market was unable to satisfy with adequate machinery. To date, our refining hammer mills have three patents for the enhancement of copper, aluminum, brass and steel deriving from waste waste, with the possibility of making an excellent economic profit from the output material.
With regard to this path, what will be the news that you will present at the 2020 edition of Ecomondo?
We are satisfied with the growing demand for refining plants and will present the latest upgrades. In addition, towards the end of 2019 we launched a monitoring plan of some of our hammer mills installed in highly intensive treatment cycles with 16-hour shifts. In this way we were able to identify new technical solutions, significantly increasing productivity and arriving, like the new 2020 Mega 1500 model, even at 30 tons / h. All this while maintaining the same energy consumption and quality of outputs .
We will present the new models of the Flex series and the Mega series. The innovative grinding concept will allow companies to think about a delta between expenses and revenues that is different from market standards, with an interesting view also on the timing and methods of return on investment.
Think about an increasingly dynamic and specialized future of the market?
Within our company, we have long started this path, effectively responding to the changes in an increasingly demanding business. Compared to the competition, we have chosen to specialize in the valorization of metal scrap thanks to the innovative hammer mills from 90 kW to 450 kW.
The continuous commitment to Research and Development allows us to boast a solid professional reputation among the companies in the sector. Our peculiarity of anticipating market needs allows us to position ourselves as a leader in the production of these machines.
We are very satisfied with the achievements: our main goal is customer growth and positive feedback confirms our work. If customers make a real profit from our products, it means that we are going in the right direction, for the companies that have chosen us and for those to come.
Interview with Guilherme Pina, owner of Ecofuturo
Interview with Guilherme Pina, owner of Ecofuturo
Ecofuturo is a young family-run industrial company. Located halfway between Lisbon and Porto, over the years it has decided to specialize in the refining of electric motors and small waste from WEEE, in order to enhance the individual granulated metals.The Owner Guilherme Pina has a clear vision of the future, both in Portugal and throughout Europe. Moving away from traditional trading activities, he preferred to invest in machinery and technologies to maximize the economic value of scrap metal. We recently had the pleasure to meet him and to know better his company , also clarifying the reasons that led him to choose the Compact Panizzolo Recycling Systems refining plant.
Good morning Guilherme. Can you tell us about yourself and the company? What is your story?
Ecofuturo was founded in 2014 in Marinha Grande, the same place where my grandfather started his business of collecting and trading metal and ferrous turnings sixty years ago. He was one of the first in this area and, probably, in all of Portugal. We have grown together with companies in the automotive sector, while the second generation has also expanded the field of action to other medium-light scrap.
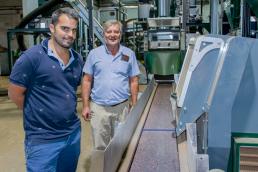
When I started to work in the company, as I deepened the dynamics of the market, I realized that investing in recycling plants offered greater opportunities to grow. The Portuguese general mentality was – and still is – strongly linked to selling as it is, and unfortunately my grandfather’s company made no exceptions. For this reason I decided to change my path and found Ecofuturo together with my parents and my brothers.
From the beginning we were able to distinguish ourselves for an industrial mentality, looking for inspiration to the most advanced European companies . The path is still long, but we have already obtained positive feedback and we aim to be recognized for the quality of the granulated metals we obtain in output. To date, 60% of our outputs are sold in Portugal, both to specialized companies and directly to the foundry.
Why this change of direction compared to the grandfather’s company?
Because in pure trade there is no longer any profit or future, especially since the "Chinese National Sword" blocked the export of waste to China in 2015. In recent years, the Portuguese and Spanish market offers good room for maneuver to invest in recycling plants and yet the specialized companies can be counted on the fingers of one hand.
Many exporters insist on looking for new outlets but the future of scrap is here, in our country, where we can re-introduce the raw material into the production cycle. The main problem, as already mentioned, lies in the general mentality. Monetary investments are of little use if there is not an owner with a clear vision and a team of competent employees.
Ecofuturo wants to be a modern company that looks to the future, investing today in innovative technologies for the recycling and recovery of secondary raw materials.
We have made our own experience and we are constantly trying to expand our commercial network, even buying scrap up to Madrid.
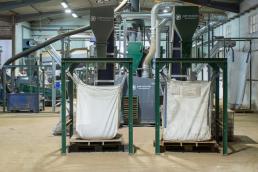
How did you start and then develop the corporate treatment cycle?
By founding Ecofuturo, I could count on the passion for the sector handed down by my grandfather, but I built my concrete experience by working directly with the material, machinery and informing myself with other recycling companies. For the first period we focused on the recycling of electrical cables and small WEEE and then, starting from 2018, we also expanded to the treatment of electric motors. We tried, with bad results, to work with Chinese treatment plants: the quality of the metals was not up to our expectations, the productivity was very low while the breakages were more and more frequent. In those years we were expanding our presence in the national and Spanish market and therefore we wanted to invest in a more performing and professional system.
Why did you choose to rely on Panizzolo Recycling Systems?
Through direct experience I’ve understood that the best investment was in the complete enhancement of the copper granulate from electric motors and small WEEE. I carefully analyzed what the European market offered, finding Italian companies very well prepared in this field. Finally, the choice fell on the refining plant of Panizzolo Recycling Systems, as it immediately seemed to me the most suitable for achieving our production and quality objectives.
Visiting Panizzolo I particularly appreciated the transparency, honesty and experience of Mauro Panizzolo and his collaborators. The company is growing thanks to its direct experience in scrap grinding, learning every day from its grinding processes and developing the treatment and refining cycles in their plant near Padua. I identify with Mauro Panizzolo a lot and I find that he has an edge over those who, without any experience, have the only goal of selling you only his product.
We chose the Panizzolo Recycling Systems plant also for the modularity of the elements and for the simplicity of maintenance. In the first case this will allow us to quickly install any upgrades, according to our production needs, while in the second case we can easily maintain a constantly high quality of workmanship.
In comparison to the previous one, what benefits have you obtained with the Panizzolo refining plant?
Before Panizzolo our refining cycle was based on a Chinese plant which caused me important limitations and problems. For example, the pre-ground from electric motors had to be processed over and over again, discarding many metals before reaching the final output. The production ratio between pre-grinding and refining was very low, about 200-300 kg / hour, with long periods of storage of both incoming and outgoing material; not to mention any delays due to the turbine being blocked. In the input there is commonly a percentage of steel, aluminum and iron which increased the abnormal wear of the blades, also causing them to break.
Today the Compact Refining plant allows me to avoid these problems. The refiner hammer mill does not fear the heaviest metals, in a single step I recover and maximize the quality of the metals, saving time, effort and operators involved.
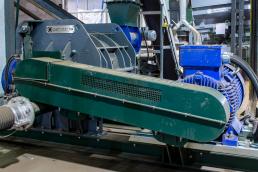
We are currently still bringing the plant to production capacity, but we have already exceeded expectations and we are sure to reach almost 1 ton / hour of processed material. Obviously everything will depend on the type of material we decide to work with. The Compact Refining plant will allow us to further expand the range of treated waste, also refining all those types of fluff that are difficult to locate both in Portugal and Spain.
Even today we are building our experience with a treatment cycle, knowing that Panizzolo provides a professional remote consulting service. At the same time I push my collaborators to build their own experience, an element that will distinguish us in the national market.
What will be the future of scrap companies in Portugal? And what are your next business goals?
In the near future, I expect to see a market increasingly oriented towards waste treatment, with the gradual disappearance of traders focused only on exports. The survival of Portuguese companies in the coming years will depend on their ability to initiate a path of professionalization both from an organizational and production point of view. The national and European market wants ever greater structuring, organization and modern waste treatment cycles for the reintroduction of secondary raw material.
At the moment in Portugal there are reasonable investment opportunities and I am convinced that Ecofuturo is pursuing the best possible path, thanks also to the high production quality of the Compact Refining Plant supplied by Panizzolo Recycling Systems. In the next few years my goal will be to expand and consolidate our presence in the Portuguese and Spanish market and, once the plant is fully operational, I do not exclude the possibility of further investing in a Panizzolo hammer mill to improve and implement the cycle. of pre-grinding of the scrap I buy.
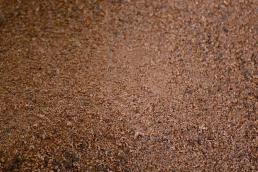
Interview with Luca Pallotti, director and commercial manager of Ferrotrade
Interview with Luca Pallotti, director and commercial manager of Ferrotrade
Located in Genoa with three offices, Ferrotrade actively acts throughout Liguria and in part of Northern Italy both in the collection and treatment of metal waste, providing a high quality secondary raw material in Italian foundries and steel mills.Reliability, seriousness and technological investment are the distinctive elements of this family-run company. Let's find out more about its peculiarities together with Luca Pallotti who, at the new headquarters, installed the Panizzolo Recycling Systems treatment plant with a stationary Flex 800 hammer mill.
Good morning Luca. What is the history of Ferrotrade and what role does it play in the national market?
We are a relatively young company but with a long tradition in the scrap trade sector. Together with my father Salvatore and my sister Patrizia, we founded Ferrotrade in 1998 starting with about 4-5 people and dealing mainly with ferrous and demolition scrap. Over the years we have gradually expanded the commercial network and expanded the range of waste, relying today on three production sites in the Genoa area and more than doubled staff.
As a sales manager, I have solid contacts with many Ligurian, Lombard, southern Piedmont and Northern Italy companies. We collect scrap from small artisans, from mechanical workshops, body shops, demolition cars, Ec-center and from large companies such as Ferrovie dello Stato, Autostrade per l’Italia and Ansaldo Spa.In addition to the treatment of ferrous scrap, thanks to the Flex 500 Mobile mill since 2012 we have also expanded to the enhancement of mixed aluminum. A company branch in constant expansion and which today sees a new mill and many new scrap in action.
Why did you choose to work with Panizzolo machines?
We have known Mauro Panizzolo since he dealt with car engines in his recycling plant near Padua. When we hit the market looking for a new treatment plant we visited their headquarters, where we were pleasantly surprised by the quality of the hammer mills.
Mauro's direct experience for us was a guarantee of quality and technological innovation, confirmed both in tests and then in daily use.
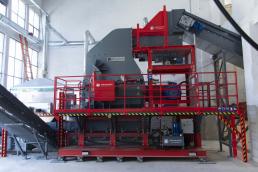
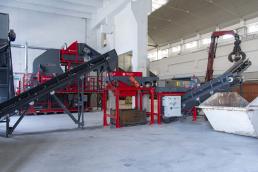
Why did you choose the Flex 500 Mobile in 2012 and what was your experience?
At the time we chose this model because it was the most versatile and compact, with a decent engine and hourly productivity. It possessed an original design, a sturdy carpentry, structured for easy transport and complete with soundproofing. In the city of Genoa, the space for us as companies is still very limited, forcing us to optimize all production and storage areas. The Panizzolo hammer mill was a choice that met our expectations also from this point of view. Another plus we found is the interchangeable cradle, allowing us in those years to have many experiences of mixed metal recycling, WEEE treatment, collection from MSW and more.
So did you find the patented interchangeable cradle very useful?
The interchangeable cradle gives Panizzolo Recycling Systems machinery an edge over other models on the market. The cradle avoids wasting time, speeds up production changeovers and makes the hammer mill a versatile machine for a wide range of processing cycles
My operators still use it a lot even in the new Flex 800 Stationary, planning certain types of grinding or refining in time. In just under an hour we can go, for example, from grinding aluminum to the treatment of WEEE.
The interchangeable cradle has allowed us, especially in this unexpected period of health crisis, to move quickly to the treatment of other more profitable materials and always producing a high quality output that can be delivered to the foundry or steel mill.
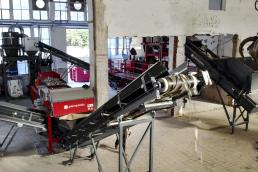
Why did you decide to switch to the Flex 800 hammer mill?
By specializing in waste treatment, year after year we have increased our purchasing pool. We mainly collect ferrous scrap, but we are also progressing well on the aluminum front, electronics from WEEE, mixed metals and separate collection from Eco-centers in the province.
In 2019 we had the opportunity to expand to a third location, activating a new storage and treatment authorization for a quantity of approximately 50 tons of waste per day. Discussing with Mauro Panizzolo we decided that the most suitable mill for our new production needs was the stationary Flex 800, with which we currently treat 5 tons / hour of mixed aluminum and whose output is subsequently enhanced with a magnetic drum, an air separator and an eddy current.
Some manufacturers claim that grinding aluminum with hammer mills is counterproductive due to the losses in dust. Given your long experience, what is your opinion?
It all depends on knowing the correct course of treatment. In this period of crisis, where many strategic sectors have reduced the purchase of raw materials, market penetration is strongly linked to the purity of the metal that a company is able to obtain.
The Panizzolo Recycling Systems hammer mill allows us to achieve an important qualitative leap in aluminum, with an economic sales value that could hardly be achieved with other machinery. To avoid unnecessary losses, we at Ferrotrade set the grids in such a way that the material is ground only strictly necessary, so much so that we currently find small quantities of aluminum powders. Moreover, if we really want to be honest, with the right commercial connections, the latter also have their own appropriate sales channel.
Why is the best direction to produce secondary raw material?
Anyone in our industry has been able to see the sudden changes in recent years. Foundries and steel mills demand higher quality every day and the market reacts accordingly, it has become increasingly difficult to market scrap that does not meet these demands.
The only solution is to invest in new treatment technologies, as we at Ferrotrade did, otherwise you risk losing the competitive advantage in both buying and selling. At the same time it is necessary that these technologies are flexible in the treatment, allowing to perform rapid production changes according to market trends.
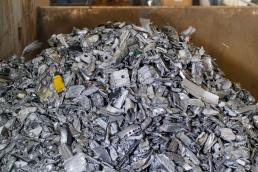
A bit like we did with the Panizzolo Recycling Systems hammer mill: today we work with mixed aluminum, but in a very short time we can switch to other metal scrap.
Do you consider that the future of the sector will go in this direction?
Absolutely, we have been investing in this direction for many years. To attest to our growth path we can boast the ISO 9001 and ISO 14001 certificates for the high quality of our production process, as well as the 333 and 715 certifications for the production of secondary raw materials. Obviously, these certificates are obtained only after considerable personal and economic investments, however today they are indispensable when you deal with many medium-large companies, both in the purchase and sale of the material.
Thanks to the Panizzolo Recycling Systems plant, we supply Italian foundries and steel mills with a product that I don’t say is the same as an ingot or billet, but it is still a high quality material ready to be melted in their furnaces. Ensuring a constant quality output is not at all simple, however the combination of our experience and that of the Panizzolo service allows us to maximize the productivity of the plant and the quality of the outputs.
2020 trade fair events
2020 trade fair events
From 17 August our offices are reopened
Don't miss our next 2020 trade fair events:
ECOMONDO
STAND 47 - HALL A3
from 3 to 6 November
Rimini (Italy)
RECYCLING
Stand H127
from 17 to 19 November
Gorinchem, (Netherlands)
POLLUTEC
-waiting assignment-
from 1st to 4th December
Lyon (France)
Panizzolo Recycling Systems software: how does it contribute to profitability in scrap treatment?
Panizzolo Recycling Systems software: how does it contribute to profitability in scrap treatment?
Panizzolo Recycling Systems integrates, in parallel with the mechanical design, the internal development of a specific software for the control and management of its recycling solutions. Why has the company structured such a specialized activity over the years?On the occasion of the recent start-up of the Compact Refining Plant, we asked this question directly to Andrea Simoni who, alongside the manager Denis Zanin, has programmed the operator interface of the recycling plant.
Hi Andrea. What is the Panizzolo software and why is it developed internally?
The software development was based on our direct experience in the treatment of metal scrap. The operator interface takes place via touchscreen and therefore we have designed simple screens of the entire treatment cycle, with an immediate understanding of monitoring and adjustments also in real time.
Owning the software and, in parallel, also the wiring diagram is essential for us. Technology is always constantly updated and external consultants could have slowed down the company’s research and development. Otherwise we can quickly install upgrades and latest generation technologies for the benefit of productivity, security and logical management. We also distinguish our attention in the translation of the entire operator interface, a necessary element to further simplify its use.
How do you go about structuring the software?
Basically, the software has a logic common to all Panizzolo recycling machines while, for more complex waste treatment plants, it includes more specific additional sections. Going into detail we find two levels of parameters. On the one hand we have the settings for essential operating safety and logic. This includes, for example, the start-up and shutdown phases where, especially in the refining plant, the electricity must be optimized and the flow of material must always be constant.
Unlike the second level, the parameters can be freely set, both during the testing phase and at a later time by the customer. The most important certainly concern the hammer mill but we also allow you to interact with other components. Specific sensors record the trend in real time, allowing the software to understand if the mill works correctly or if it must intervene to restore production balance. The parameters are always editable, even in real time, and are located in a special section called “Recipes”.
What is the operating logic of this section?
In a few words, we confirm what distinguishes Panizzolo recycling machinery: quality of the outputs and flexibility of treatment. In our experience, we know that scrap, in addition to diversifying into categories, is never homogeneous in composition. A concept as simple as it is fundamental. For this reason we have developed the “Recipes” section.
The customer clearly and intuitively displays the fundamental parameters, personalizes the types of treatment and can also make changes during processing.
I try to explain better. It happens that the need to work or test other types of material emerges in a company. Instead of changing the parameters used for daily processing, it is possible to select a new recipe and set completely new data. Once confirmed, these parameters can be unique with personalized names.
As already mentioned, the refusal at the entrance is never completely homogeneous. Through the recipes we allow to regulate loading and flows, so that mill and separation systems can optimize all treatment steps. On this topic, during the training of the Compact Refine Plant, we clarified the meaning of "processing optimization" for Panizzolo.
With our software we don’t just want to avoid overloading the machinery but we want to allow continuous and balanced processing, which is able to bring benefit to final quality, hourly productivity and component integrity.
Does training therefore play a fundamental role?
Absolutely. During the testing phase, we optimize the first recipe together with the customer and his operators. We are already able to load our predefined treatment parameters, however once in the field and with the actual scrap we proceed to confirm these calibrations. We follow a precise procedure, bringing the production to a steady state and explaining every single step to the operators: what parameters to touch and how they influence, what we recommend keeping an eye on, how to intervene according to the situations and much more. Our goal is to provide a solid starting point and allow customers to build their own experience. With the testing of the Compact Refine Plant we pay more attention to these phases, as each component is designed to bring a certain production benefit.
In addition to your experience, how does the software help you in training?
The monitoring graphs allow you to better clarify the grinding of the hammer mill. If the treatment cycle is a continuous start and stop, at the end of the day or at the end of the month, the software will highlight the accumulation of work vacuums, confirming the gap between working hours and actual production.
Always the graphs allow you to maximize productivity and at the same time avoid overloading or blocking the mill. With the training we try to pass as much information as possible to the operators. However, if the customer has specific needs, we are always present with advice and assistance in post-sales.
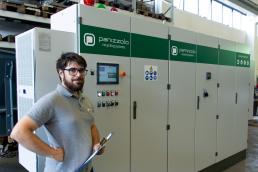
What are the benefits of Panizzolo software for maintenance?
In case of malfunctions, the software indicates the area to be checked, attaching an explanation of the problem and avoiding the operator to waste time with generic alarms. Specific warnings appear periodically for routine maintenance, the execution of which must be confirmed manually, and then remain stored in the internal memory. Being owners of both the software and the wiring diagram, we are doubly efficient on the assistance side. We have full competence of all the electronics installed, even if only trivially for a matter of spare parts, while the control panel is supplied already prepared for internet connection for remote assistance.
What improvements are you planning for the near future?
At Panizzolo Recycling Systems we care a lot about the constant electrical, electronic and software updating and therefore for this reason we have a lot of projects . Without going into too much detail, we are focusing a lot on remote assistance, much appreciated by our customers. We have recently introduced a new generation touchscreen, programming a series of updates and implementing new parameters.
Together with the manager Denis Zanin, we plan the implementations while remaining anchored to a logic of simplicity and immediate understanding. The software must always adapt to the production cycle, the purpose of which is to optimize and maximize both the production potential of the machinery and the quality of the output metals.
Environmental certification: a competitive advantage for waste recovery and treatment companies?
Environmental certification: a competitive advantage for waste recovery and treatment companies?
Since July 2015, the transition of the Panizzolo waste treatment plant to the Integrated Environmental Authorization (A.I.A.) has added an important element to the business development plan. With the expansion of treated waste and the investment in new designs, the company can now boast an End-of-Waste treatment cycle with its own patented hammer mills.
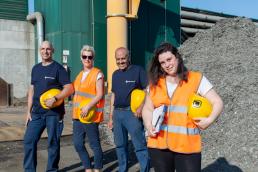
Good morning Beatrice. Can you explain your role and how you operate in relation to the Integrated Environmental Authorization?
Taking on the role of Head of security and corporate certifications, I took over from Piove di Sacco in conjunction with the application process for AIA authorization. It is not immediate to understand how an authorization mechanism works and, consequently, to manage the whole certification process. Each company is different but it has been a very stimulating and challenging experience.
Together with the consultant we studied the activity on several fronts, both from an environmental and production point of view, thus conforming many macro areas with respect to the directives. In particular, we have more defined the role of the staff, whether working in the office or on the construction site. With this in mind, we have all participated in many training days, an activity that we are still pursuing both to create awareness and to confirm our preparation. In carrying out my work, the most important thing is to involve all the operators concerned with adequate training, information and indicating an operational direction.
What pluses does ISO 14001 allow us to obtain?
The ISO 14001 certification procedure ran parallel to the A.I.A., which actually entered into force in 2016. We took this path because it provided us with many benefits and a professional working methodology for achieving the A.I.A. objectives. Alongside the more traditional controls, new registers have been added for monitoring the consumption of raw materials such as oil, diesel, electricity and more. In doing so, we gained greater awareness of how ecological and economic costs impact on each waste treated.
On the other side, our customers are sure to buy a metal treated with certain quality standards. Increasingly suppliers and customers, especially foreign ones, prefer to relate to companies holding these certifications. A number that will surely increase in the coming years, given that companies also gain greater authority before the state control bodies.
The certifications are regulated, therefore they must be confirmed annually and are subject to updates. In fact, with the maintenance visit in April 2020 we moved to ISO 14001: 2015 certification. This year with the COVID-19 emergency was doubly demanding, having to do everything remotely.
Can you better explain the company’s environmental policy?
ITogether with the ISO 14001 certification, the company has formalized this internal document, where we become aware that our business has an impact on the territory and, consequently, we formalize a series of future programs for work improvement. Also for this reason Panizzolo has invested in the refining plant for metal waste.

Unlike the blade turbines or cell turbines on the market, our patented refining mills achieve an output with a degree of purity that is difficult to compare in the sector. A plus that allowed to integrate the European certifications 333-2011 and 715-2013, attesting the production of secondary raw material.
But what does it mean to be certified as producers of raw materials?
Virtually certification works this way. During the treatment cycle the material must be checked and comply with certain standards, including a percentage of purity defined by the European guidelines. Specific internal reports are compiled periodically and meticulous checks are performed on the granule of secondary raw material obtained. When the raw material is transferred to the customer it is always accompanied by our declaration of conformity, indicating the respective European code.
When the company produces second raw materials, it increases the economic value of metals and in doing so, it also obtains greater administrative simplicity. The output is no longer managed as waste, therefore the complicated procedures of the unloading form are replaced with a simple delivery document. Obviously all this could not be done if upstream there was no ISO certification attesting the quality of treatment of the metal waste.
Many customers visit the treatment plant when they have to evaluate the purchase of Panizzolo Recycling Systems products?
Yes it happens many times. Besides being important to see our production line in operation, I have often seen a lot of interest in the quality of the outputs. They often ask me to see the second raw material certificate. Honestly, it is a lot of fun to see their amazement in comparing the granulated copper in output compared to the input waste. However, in general, companies want to visit us to confirm our professionalism, knowing that we are one of the very few companies that is both a manufacturer and a user.
How do you see the future of certifications? And what will be the next steps of Panizzolo Recycling Systems?
I think that in the coming years we will see an increase in the number of certified companies. All our customers and suppliers are, even the smallest ones. The European Union is also an additional factor pushing more towards end-of-waste treatment cycles and the reintroduction of the second raw material into the economic cycle. In Panizzolo Recycling Systems for the near future we are considering to implement the certifications of the Arzergrande headquarters. We are currently in the analysis phase, but we will soon identify the most relevant typology.
Interview with Federica Foterni, owner of West Recycling
Interview with Federica Foterni, owner of West Recycling
West Recycling represents one of the major historical companies in Sardinia for the recycling of metal scrap, with a special focus on the recovery of WEEE electronic waste. The company is located near Cagliari and it receives both waste from urban centers and from industries.
In a sector where most of the entrepreneurs are male today we would have the pleasure of interviewing Federica Foterni, owner of West Recycling. With an enviable entrepreneurial charisma and constantly updated on the latest news on the world of recycling, Federica Foterni will explain to us how the company has distinguished itself over the years and what its future goals will be.
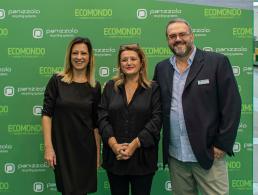
Good morning Federica. Can you tell us about yourself and the company? What is your history?
I state that my family has been operating in the metal and waste recovery sector for over 40 years: my father, who unfortunately passed away 10 years ago, has been involved in the recovery of ferrous and non-ferrous metals for years and at the end of the 1980s he was among the very first Italians to recycle heterogeneous and homogeneous plastic. So let’s say that, in a way, working in the waste recycling sector was almost natural.
West Recycling‘s experience and bet in the market for the recovery of durable goods (better known since 2005 with the acronym WEEE) was born at the end of 2001 and it expanded in 2008 with the introduction of treatment lines refrigerators and other discarded electronic equipment. My company can therefore boast of having been the first recycling plant for the treatment of WEEE in Sardinia.
What are the peculiarities that distinguish you in the market?
The world of WEEE electrical and electronic waste is particularly heterogeneous. Potentially any authorized company that has the corresponding EWC can carry out the treatment of WEEE waste by applying only the “minimum” rules. West Recycling wanted to go one step further.
Since 2008 we have adhered to various types of regulations. We follow the provisions of the WEEE Program Agreements, the WEELABEX European standards and the Accreditation protocols dictated by the WEEE Coordination Center. From the first moment, it was a source of pride and satisfaction for us to have accepted all these challenges and, thanks to the commitment of all the working and administrative components, to have fully achieved all the objectives set by the regulations.
What kind of recycling plants do you work with?
Over the years we have developed several WEEE treatment lines. In the refrigeration and large white treatment line, we use the Panizzolo OPH Opener, in order to perform efficient shredding of scrap such as washing machines, dishwashers, ovens, kitchens and much more. In addition, we also have a smaller industrial and household electrical and electronic waste treatment plant, belonging to the category of R4. The Panizzolo treatment cycle allows us to enhance the metal content through the Flex 500 mobile hammermill in combination with various separation systems.
Which companies do you relate to for the purchase of waste and the sale of outputs?
Our supply market consists mainly of municipalities and WEEE consortium as well as, having an additional line dedicated to the treatment of ferrous scrap and motor vehicles, from producers of such waste such as industries, scrap dealers and car dealers.
Considering that our aim in the scrap market is to conclude the waste recycling cycle, the great majority of our outputs are sold as secondary raw materials directly to the steel and foundry. The remaining part, consisting of a mixture of metals and aggregates, is sent to other national companies to complete the treatment. However, I plan to complete these inert treatment cycles within West Recycling.
Can you tell us about the ASSORAEE association to which you are registered?
ASSORAEE brings together the most important Italian WEEE recovery and treatment companies. In recent years the Association has committed itself above all to the creation of tools such as the A program Agreement between WEEE plants such as ours and the Consortia that collect this waste. In addition, the companies that are part of it are assisted in the implementation of their production processes to the standards prescribed by the European Union with the aim of reducing environmental impacts and raising the quality in the management of WEEE.
What benefits have you obtained with Panizzolo machines?
For many years we have been using the OPH Opener, the Flex 500 mobile mill and all the separation accessories, to perform high-performance grinding and refining of WEEE waste and obtain an output that distinguishes us in the market for its high quality. One of the characteristics that I immediately appreciated was the accuracy of the design. At the time, I carried out an in-depth analysis also from the point of view of those who would have worked on it in contact with the recycling machinery every day. In my opinion, the quality of a machine must also be extended to the ease of use and the reduction of downtime for the change of hammers, parts subject to wear and tear, ordinary and extraordinary maintenance.
From these points of view, I found a valid technological supplier in Panizzolo Recycling Systems. The machinery, the recycling plant and the flow logic have been designed to be functional for those who will have to work directly on them and not for those who simply have to see it to third parties. Benefits that I am still experiencing and that allow me to reconfirm Panizzolo also for future projects.
What do you think of the design of the Panizzolo hammer mills and the patented interchangeable cradle?
As I said earlier, I particularly appreciate the design of your hammer mills and I believe that the interchangeable cradle is an exceptional solution. The replacement times of the grids and hammers are very short, allowing us to have a particularly efficient system from the point of view of production and cost.
In recent months there have been major changes due to COVID-19. What future lies ahead for the sector?
The scrap metal sector, including WEEE waste which is no exception, is the litmus test of a country’s economic prosperity. It will depend a lot on the measures put in place by the Government and Regions to start up the Italian production sectors again. Obviously, in a modern globalized context, everything will also depend on the provisions of the European Union and, more generally, on the decisions of the United States and the Asian market.
What are your plans for the near future?
Earlier this year, before the lockdown, we started a feasibility study to implement a new production line in West Recycling. In this way I want to enhance the residues from my WEEE and scrap treatment plants, completing the enhancement cycle and obtaining secondary raw material.
Given the excellent relationship with the Panizzolo Recycling Systems machinery, I performed a test with your refining plant and obtained excellent results in terms of purity of outputs and ease of use. The future will be more and more in End-of-Waste treatment and we intend to take this path as soon as possible using the Panizzolo refining solution.
Maximize the investment with Panizzolo Service
Maximize the investment with Panizzolo Service
Panizzolo recycling solutions offer a wide range of industrial waste treatments with maximum flexibility of use. However, the composition of metal waste can cause our customers difficulties in regulating the treatment itself.
It ‘s therefore essential for the company to use the best after-sales tools, allowing a correct transfer of knowledge and the right balance between profitability, wear and energy costs.
Let’s talk about it with Mauro Bassan, Service Manager at Panizzolo Recycling Systems.
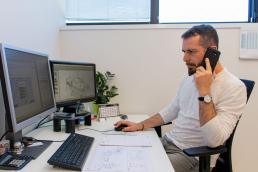
What are the goals of Panizzolo service? And how did you deal with the COVID-19 problem?
Remote assistance has enabled the after-sales services to be active at a time when direct interventions were not possible due to the COVID-19 pandemic, especially abroad. In recent weeks, however, we are also returning fully operational on this front.
Often we activate special web assistance channels for production consultancy, setting up the industrial waste treatment plant for new waste, maintenance, processing suggestions. Over the years we have outlined precise communication ethics with customers: professionalism, transparency in relationships and intellectual honesty.
In accordance with these objectives, the Panizzolo Recycling Systems service cannot focus only on the sale of spare parts. Our task is to lead the customer to full awareness of the production potential of the recycling plants he works with.
Can you better explain what you mean by remote service?
By appointment, it is possible to contact one of our technicians by telephone, LAN connection of the machine and new technologies available soon. With the remote service, or web, we give customers the opportunity to interface in a clear, simple and intuitive way. We can intervene to check the recycling machinery, inspections, general clarifications, 360-degree treatment suggestions and much more.
Let me explain through a practical example. A few days ago one of our customers contacted us asking for a couple of hours of advice to treat a new metal scrap because he wanted to find the best setting. I state that he is not new to the job, rather he has been working with our mobile mill for many years. He therefore sends us the photos of the metal waste, also explaining how he would have liked to set the grids to obtain a high quality output proler. Analyzing everything, we therefore corrected the configuration and parameters of the mobile mill, directing it to a more gradual and safer start. With the next appointment we will connect to the plc of the mill and complete the setting together, so that we can optimize it in real time.
It is not unusual for me to see that many customers, despite having their experience, continue to search for our advice. We even receive official thanks by emails for exceeding their production expectations
What can you tell us about original Panizzolo Recycling Systems spare parts?
Being both builders and direct users allow us to know exactly how metal castings and mechanical components will behave during processing. For this reason, Panizzolo original spare parts are designed to achieve always maximum production results.
There are cheaper options on the market, often improvised, which can lead to serious production problems. Our special melting hammers, for example, were developed together with the University of Padua both to guarantee constant quality and to eliminate the inherent problems of the more commercial models
In fact, we have found that some alloys risk abnormal wear or, worse, deformations of the structure which lead to important vibrations throughout the machine. Exactly a fact that one of our customers has experienced recently. This company, attracted by an affordable price, relied on a supplier who completely ignored the final field of use of the recycling machine. The inappropriate alloy consumed the hammers in a few weeks, deforming and locking them inside the rotor. Due to the vibrations, the hammer mill no longer guaranteed safe processing and we had to act promptly to avoid further negative consequences.
Are these peculiarities also found in other parts of the recycling machinery?
Absolutely. When you think of components subject to wear, you often imagine blades, hammers, armor or grids. However, grease also belongs to this category, especially the one used in rotor bearings. For the constant efficiency of the hammer mill it is essential to preserve the bearings over the long term.
In our recycling plant located in Piove di Sacco, we have tested different types of grease for high temperatures, choosing a special mixture in collaboration with a highly qualified Italian company. In comparison with other more commercial brands, it guarantees greater lubrication cycles, respects the integrity of the bearing in the long-term, reduces the operating temperature and, more importantly, does not fear metallic dust.
Just the other day I had the opportunity to discuss it with one of our customers. He wanted to find an alternative brand in his Country and was convinced that it would be enough to use the same grease applied in pellet mills and briquetting presses. However, I had to dissuade him from using it and explain to him that it would lead to problems with viscosity, heat point and mixing compatibility. Unfortunately, many people think that lubricating greases are all the same, which is absolutely wrong. Over the years I have been able to observe, also in other sectors, bearing breakages resulting from the lightness attributed to lubrication.
Are you planning any news in the near future? Can you tell us something?
As I told you at the beginning, during this year we will introduce implementations to the customer service. Come accennavo all’inizio, nel corso di quest’anno introdurremo delle implementazioni al servizio di assistenza. Obviously I can’t go into too much detail now, however I can anticipate something
In recent years, after-sales activities have seen an exponential increase in remote requests, customer interventions and spare parts sales.
We want to continue maintaining a high quality of service and at the same time remain consistent with our business goals. With this in mind, we are both investing in the internal organization and in the development of new technologies at the service of scrap treatment companies.
Remote assistance, starting from 2020, will be increasingly used and therefore we are completing the preparation of a new technology very useful for the customer and very simple to use. I can not say more, but in the coming months we will publish all the news of the Service Panizzolo.
Interview with Richard Groß, general manager of PIP Processing In Plastics
Interview with Richard Groß, general manager of PIP Processing In Plastics
Next to the well-known scrap treatment companies there are highly specialized industrial realities. They do not treat aluminum profiles or electric motors, but they preserve the environment and they produce second raw material starting from plastic and aluminum caps.
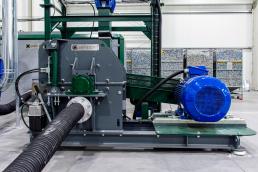
As required by the German government, empty water bottles must not be thrown in the waste; rather they must be recovered from the factories of origin and, once washed and sterilized, they are refilled. The system has been successfully adopted in Germany for many years. The only drawback however is the cap, which must be replaced to maintain a high quality of bottling.
This waste is currently being collected and processed by PIP Processing In Plastics. Founded in Rheinböllen in 2009, the company is structured to work in an End-of-Waste cycle and it produces high quality second raw materials to protect the environment as well. Let’s discover the peculiarities of this company together with General Manager Richard Groß, who recently chose the Panizzolo refining plant for the treatment of its aluminum caps.
Can you tell us about PIP and its peculiarities?
In PIP Processing In Plastics we process caps from German bottling companies, producing high quality second raw material output. Thanks to our strategic position close to these companies, we safeguard the environment by limiting traffic and completing the treatment within our factory.
A whole cap that travels on the road produces much more pollution than the same in granulated version. To our customers we sell aluminum granules and plastic granules divided into polypropylene and polyethylene.
I see that you have hung many environmental quality certificates
They certify how annually we are committed to protecting the environment. Our privileged position allows us to reduce CO2 for the transport of waste. We also aim to optimize transport every year, in order to save more and more carbon dioxide in the environment.
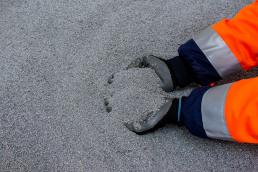
Tell us better about the waste you recover
Until twenty years ago, waste from bottle caps ended up in landfills or incinerators. However, over the years we have become aware of the potential to reintroduce them in the economic cycle. Founding the activity I focused on the quality of the outputs, so as to differentiate myself from the other German competitors.
We have a plant dedicated to the treatment of plastic caps. They are separated from the metal ones, then shredded and then washed. Once all foreign contamination has been eliminated, they are divided into our two qualities: polypropylene and polyethylene.
The plastic treatment line is divided into separate lanes. This is because many times we also buy caps from production waste, which need a different treatment.
Can you explain better what you mean by the quality of the outputs?
The main part of our business is to choose the product to be treated, knowing what we want to achieve in output. Buying new grain is not cheap at all, but with our products we are able to offer a raw material about 25-30% cheaper, maintaining a quality almost comparable to the new one. In this way we can offer our customers a double benefit: savings in purchasing and knowing that they are using a raw material from recycling plants. Important thing in the market, as -German companies are increasingly sensitive to this issue.
Generally we sell to big companies that mix the mixture and blend it to create new products. A part of our customers, who purchase plastic and aluminum granules, works in the automotive sector. Depending on the case, they can be used to produce mudguards, sides, engine covers and more.
Are you the most convenient on the market?
Absolutely not. Around it is possible to recover granules cheaper than ours, but they do not have the same quality. They have large percentages of impurities that can damage the production of our customers at the time of mixing and melting. The reason is given that the input from their plants comes from different scraps, while we are very selective in purchasing.
Our customers keep coming back because they know they find high purity percentage of polyethylene and polypropylene. In fact, the companies that offer lower quality tend to export abroad, while our products are intended for consumption by the German industry, which always requires higher quality
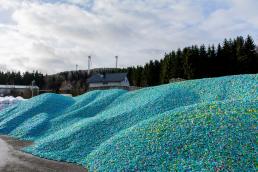
Aluminum caps instead of what procedure follow?
Until recently, aluminum caps were only separated and then destined for treatment in other companies very distant from Rheinböllen.
We obviously realized very early that this way of working was counterproductive both for our business and for our vision of environmental conservation.
Furthermore, we have also seen that the market has been changing in recent years. Some time ago aluminium caps were replaced with plastic ones. However, an increasing environmental sensitivity is changing direction, preferring the use of metal ones. In 2019, for example, the amount of aluminum caps in Germany has grown by 8% and will increase more and more in the coming years.
For this reason, we have decided to internally manage the entire treatment cycle and be consistent with both of our business purposes: Maximize enhancement and help the environment.
An aluminum cap is more expensive to manufacture than a plastic one, however the end customer is increasingly sensitive and prefers to buy environmentally friendly products. The manufacturing companies adapt to this trend and therefore in the near future we will see more and more metal caps.
So the decision fell into a refining plant.
It was the best choice. We went on the market and looked for a supplier that had an excellent reputation and solid experience in waste recycling, especially in the refining of aluminum.
Panizzolo Recycling Systems was suggested to me by asking colleagues and friends from the sector. I was introduced to Mauro Panizzolo, who accompanied me to see his treatment plant near Padua, in Italy.
Having contacts in the peninsula, I asked around and received very positive feedback.
After a test with our material, we convinced ourselves that Panizzolo was the most suitable partner for our needs.
Seeing what the refining plant was operating what was the idea? What about Panizzolo and the outgoing granule?
I am completely satisfied with the system and with how we have been followed in all phases, from the layout to the training of my men.
To be honest there are two aspects that have positively affected me: the fact that it produces little noise and that it does not scatter dust around. All pluses that allow us to work safely with the environment and with staff without having to add other investments.
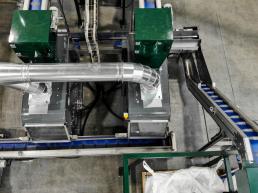
Another thing that pleasantly surprised me is the ability to customize the parameters of the management and control software. A remarkable flexibility and speed of adaptation which is perfect for our types of input waste.
Their technicians are professionally highly trained and they have given to me and to my men all the information to do their best.
Obviously now the most important part is to create our experience, in order to optimize all the functions and set-ups. However, I don’t think there will be any major problems. It is our first time with such a system, but seeing it at work, I am sure there are excellent business prospects.
Have you also seen other recycling plants?
Yes, we had seen another. It was a German company, but in the end it did not have much experience in refining. We also did some treatment tests, but the output quality did not live up to what we wanted.
In Germany how many companies are working this kind of waste?
We are not many in this field. Across Germany there should be a maximum of four or five. There are large companies that treat caps, but only because they collect many types of plastic and metal waste. They are not specialized like us, who produce high quality output. This really makes a difference.
What makes you unique in the market?
What, in my opinion, makes us unique in the German market is the fact of making the most of the metals and plastics coming out of our plants. My customers are interested in using recycled raw materials however they want to maintain a high quality of mixing and melting. Both for the plastic and for the aluminum we help them to assist business and environmental protection.